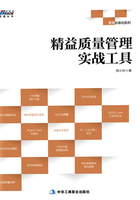
第五节 生产线平衡分析及案例
一、生产线平衡分析定义及计算
(一)生产线平衡分析定义
Productionlinebalanceanalysis,中文翻译为生产线平衡分析。众多厂家将此方法称为“LB”,即Linebalance,或“LOB”,即Lineofbalance,分析改善法。生产线平衡是指构成生产线各道工序所需的时间处于平衡状态,作业人员的作业时间尽可能保持一致,从而消除各道工序间的时间浪费,进而取得生产线平衡。生产的全部工序均衡,调整作业负荷和工作方式,消除工序不平衡和工时浪费,实现“一个流”,如图5-14所示。

图5-14 实现“一个流”
(二)平衡生产线的意义
平衡生产线可以综合应用到动作分析、layout(布局)分析、搬动分析、时间分析等IE手法,提高全员综合素质,并且在平衡的生产线基础上实现单元生产,提高生产应变能力,对应市场变化实现柔性生产系统。减少单件产品的工时消耗,降低成本(等同于提高人均产量)。减少工序在制品,真正实现“一个流”,提高作业及设备工装的工作效率。
(三)生产线平衡的计算

生产线的平衡损失率=1-生产平衡率
企业基本要求生产线平衡率需达到85%以上。1.如何识别瓶颈岗位(木桶理论)

图5-15 木桶理论
木桶蓄水容量的大小取决于最短的那块木板(如图5-15所示),在生产组装线中,整条生产线的生产效率取决于最慢的工序。
A产品通过B产品前端到①处所需要的时间,我们将该时间也称为A产品的CT(Cycle Time)生产加工总时间,如图5-16所示。

图5-16 生产加工总时间
(四)建立山积表及平衡分析
将各分解动作时间,以叠加式柱形图表现的一种研究作业时间结果的手法,如图5-17所示。

图5-17 山积表
工时测定分析(浅色为作业的时间,深色为失去平衡的时间)如图5-18所示。

图5-18 工时测定分析
二、生产线平衡分析的基本步骤和案例
(一)生产线平衡分析的基本步骤
生产线平衡分析的基本步骤如图5-19所示。

图5-19 生产线平衡分析的基本步骤
改善方法主要采用ECRS动作经济原则:
(1)Elimination——取消。
(2)Combine——合并。
(3)Rearrange——重排。
(4)Simplify——简化。
案例1:缩短生产节拍,维持人手不变
缩短生产节拍,将工序2里一部分可抽调的时间转至工序3中,以缩减整体的生产节拍,如图5-20所示。

图5-20 缩短生产节拍
案例2:减少1人,维持生产速度不变
将工序3里的工作时间分配至工序2、4及5之内,从而工序3里的人手可调配到其他生产线。可行性:工序2、4及5内均有足够时间接受额外工作,如图5-21所示。

图5-21 减少1人,维持生产速度不变
案例3:减少2人,维持生产速度不变
降低线体速度,减少生产产量。因生产需求量降低而降低线体速度。将工序3、4的工作时间分配至工序1、2、5里,从而工序3、4工作岗位的人手可调配至其他生产线,如图5-22所示。

图5-22 减少2人,维持生产速度不变
(二)生产线平衡分析案例分析
电子电装7人柔性线:
表5-15 改善前各工位的作业时间

电子电装7人柔性线,改善前各工位的作业时间如图5-23所示。

图5-23 改善前各工位的作业时间
生产线各工位的分析如表5-16所示。
表5-16 生产线各工位的分析

改善前,生产线平衡率=(18+16+24+37+45+16)/(37×7)×100%=60.2%(改善前节拍为37秒)。
改善前生产线各工位平衡图如图5-24所示。

图5-24 改善前生产线各工位平衡图
改善前的主要问题点:
(1)各工序之间不平衡导致堆积。
(2)工序的杂事多(非附加价值作业)。
(3)各工位分工不合理。
主要采用的改善方法有作业重新布局及采用动作经济原则ECRS。
表5-17 改善后作业时间表


改善后各工位工时如图5-25所示。

图5-25 改善后各工位工时
改善后节拍为46秒,减少4名作业员,生产线改善前后指标的比较:(1)生产线平衡效率提升了51%,如图5-26所示。

图5-26 生产线平衡效率提升了51%
(2)生产线人员数量减少了4人,如图5-27所示。
(3)生产效率提升了12.1%,如图5-28所示。

图5-27 生产线人员数量减少了4人

图5-28 生产效率提升了12.1%