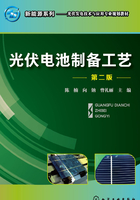
第四节 制绒不良片案例分析
制绒过程中出现的不良情况,主要有表面污染、表面发白、表面发亮、腐蚀不均、无绒面等情况。
1.表面污染(图2-9,见书前彩页)
(a)图中出现的是硅片表面有指纹残留。出现的原因是在包装时人为地接触硅片。解决的措施是添加IPA。IPA可以起到一定效果,但是不能杜绝,需要硅片车间的配合。
(b)图中出现的是硅片表面有大量的药液残留。出现的原因是IPA添加过多。解决的方法是重新进行清洗。
(c)图出现的是在同一批片子中相同位置有类似于油污的污渍。出现的原因主要是来料问题,可能在硅片包装时引入。解决的方法是与硅片车间协商解决。
(d)图中出现的是表面污渍。出现的原因主要是在制绒后反应的残留。解决的方法是重新进行清洗。
2.硅片表面颜色(图2-10,见书前彩页)
(a)图中出现的是硅片表面发白。出现的原因主要是制绒的时间不够,解决的方法通常是延长制绒时间。
(b)图中出现的硅片表面发亮,表面发沙。出现的原因主要是KOH过量或者制绒时间过长。解决的方法通常是适当降低碱液的用量及制绒时间。
3.绒面状况(图2-11,见书前彩页)
(a)图中出现的是表面腐蚀不均、硅片表面部分区域发白、有彗星现象发生。出现图中现象的主要原因是IPA偏少。解决的方法通常是适当增加IPA的用量。
(b)图中出现的是制绒后硅片表面出现绒面不均匀。出现图中现象的原因可能是来料问题。解决的方法通常是适当延长时间,可以一定程度上减轻该现象。
(c)图中出现的无绒面或表面有流星雨现象发生。出现图中现象的原因主要是来料问题。解决此类现象的措施是加大碱液用量。
(d)图中出现的绒面不均现象主要表现为部分区域绒面良好,部分绒面表现为较难腐蚀。出现图中现象的原因主要是来料问题。解决此类现象的方法是加大碱液与IPA的用量,具体加入量依据实际情况而定。
制绒过程中,常出现的不良现象是由很多因素造成的。对于常见的问题可以采取以下一系列的措施,减少不良现象地出现。
①插片 在制绒过程中,由于晶体中的缺陷,杂质和掺杂浓度将对各个晶面的腐蚀速率造成影响,因此在插片的过程中尽量保证同一花篮中的硅片来自同一晶棒,在不能保证同一花篮中的片子为同一批号时,则将批号中字母标识相同的放在一起。
②抽检 在制绒进程中如发现制绒不稳定,应在制绒时间将到时,从溶液中捞取一些片子,进行制绒效果观察,以决定是否需要适当延长制绒时间,在硅片进入清水槽后应适当进行抽样,以决定下一批次药液的补给量。
③不良片的判断以及改进步骤 由于在制绒过程中,绒面不均占大多数,因此解决这类问题为提高绒面优良率的关键。绒面不均有多种原因,主要包括刻蚀时间不够、IPA加入不足、NaOH不足等,可以通过一看二算三判断的方法来解决。首先观察不良片可以归为哪一类,其次计算硅片的腐蚀厚度以及剩余厚度,最后来判断属于哪种原因,然后采取相应的对策。
④硅片来料控制 由于位错将对制绒效果有影响(标号A和B的晶棒分别代表无位错和位错的晶棒),因此需要与硅片车间协商,在包装时,不能将标号A和B的晶棒混放在一起(100片小包装),将同一晶棒标号相同的硅片尽量放在一起,并将标号相同的放在同一箱内。