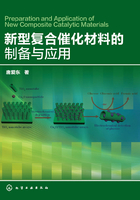
3.2 V2O5/VOSO4系列催化剂的制备及催化性能
3.2.1 概述
目前脱除工厂废气中二英主要有高温分解、活性炭吸附、催化分解等技术,其中催化分解具有脱除率高和毒害物分解彻底等优点,是工厂烟气末端治理的关键技术,相关文献报道以V2O5-WO3/TiO2为主的脱硝催化剂可用于降解二
英类有毒的环境污染物,但催化分解系统运行成本高阻碍了这一先进技术在中国市场的推广使用,高昂的催化剂价格是影响催化分解系统的主要因素,其中催化剂制备工艺及活性物质的用量对催化剂的性能与成本有很大的影响,因此,寻求新型高效低成本催化剂仍是环境工程与工业催化领域的研究热点。文献[19]报道,以VOSO4为活性成分的钒系催化剂可分解、净化极低浓度的二
英,为了查明VOSO4具有活性的原因,我们制备了V2O5/VOSO4催化剂,以邻二氯苯(o-DCB)为模型污染物研究该催化剂的催化活性,在此基础上,制备V2O5/VOSO4-TiO2-BaSO4催化剂,研究负载后该催化剂的催化活性,此外,还制备了Co2+、Mg2+、Fe3+和Cu2+掺杂的V2O5/VOSO4-TiO2-BaSO4催化剂,考察不同离子掺杂对o-DCB去除率的影响,为下一步制备以V2O5/VOSO4为活性成分的新型高效、廉价的催化剂寻找依据。
3.2.2 催化剂的制备及其表征
3.2.2.1 化学试剂
主要化学试剂见表3-1。
表3-1 主要化学试剂

3.2.2.2 实验仪器及设备
主要实验仪器及设备见表3-2。
表3-2 主要实验仪器及设备

3.2.2.3 制备工艺
V2O5/VOSO4(V/VOS)催化剂的制备:称取NH4VO3放入300mL的烧杯中,加入100mL去离子水,在400r·min-1的转速和80℃下搅拌30min,待NH4VO3溶解后,加入H2C2O4·2H2O和(NH4)2SO4,搅拌至反应液蒸发浓缩并于100℃干燥12h后,转移至马弗炉中煅烧。
制备的工艺流程如图3-1所示。以V2O5/VOSO4为活性成分,采用浸渍法制备V2O5/VOSO4-TiO2-BaSO4(V/VOS-Ti-Ba)和不同离子掺杂的X-V2O5/VOSO4-TiO2-BaSO4(X-V/VOS-Ti-Ba,X=Co2+、Mg2+、Fe3+、Cu2+)催化剂。

图3-1 V/VOS的制备流程
3.2.2.4 催化剂物性表征
本实验中,使用X射线衍射(XRD)、扫描电镜(SEM)、傅里叶红外(FT-IR)、差热分析(DTA)和热重分析(TG)等技术对所制得的催化剂进行表征,从而可以进一步研究催化剂的表面性质、微观结构及其与催化活性的关系。
XRD分析采用RIGAKU DMAX 2550/2550VB+ 18kW转靶X射线衍射仪(德国产)进行分析。工作条件:管压40kV,管流150 mA,Cu Kα线,λ=0.154056nm,采用石墨单色器,步宽0.02°,停留时间0.075 s,扫描范围10°<2θ<80°。扫描电镜(SEM)观测在日本JEOL公司 JSM-6360型扫描电子显微镜上进行。DSC-TG分析使用TGA/SDTA85le,METTLER TOLEDO进行测试。控制气氛为静止空气,升温速率为10℃·min-1,温度范围25~800℃。使用Nicolet Nexus670光谱仪测定催化剂的红外光谱。在2cm-1的分辨率采集100个扫描点。
3.2.2.5 催化剂活性表征
采用自制的动态固定床反应器进行催化剂活性测试。称取约0.43g催化剂,用氧化铝微球混匀装填于L=500mm、ϕ内=0.5mm的反应管中,两端用玻璃棉和氧化铝微球装填固定。用空气压缩机将o-DCB气体带出,导入预热混合系统,再进入催化反应炉中。用气体流量计控制气流速度(150mL·min-1),采用10mL丙酮为溶剂吸收o-DCB,吸收时间均为5min。催化剂活性试验装置图见图3-2。

图3-2 动态固定床反应器示意图
1—空气压缩机;2—空气流量计;3—液态邻二氯苯;4—催化反应炉;5—吸收瓶(催化降解前o-DCB的吸收);
6—吸收瓶(催化降解后o-DCB的吸收);7—尾气吸收瓶;a—气体预热管;b—催化剂填充管
采用日本岛津气相色谱仪(GC-2010)由氢焰检测器(FID)检测分析采集的丙酮样品,气相色谱条件如下:用30m长的毛细管色谱柱分离,载气为氮气,载气压力为0.60MPa,色谱柱箱温度130℃,汽化室和检测器为260℃,分流比20∶1。通过外标法定量测定邻二氯苯的浓度。在测试催化剂活性之前,先做空白试验,确保入口和出口气体浓度一致,再进行催化活性测试,并采用式(3-1)计算邻二氯苯的去除率:
o-DCB去除率=(入口气体浓度-出口气体浓度)/入口气体浓度×100% (3-1)
3.2.3 催化剂的表征
3.2.3.1 差示扫描量热-热重(DSC-TG)
图3-3是V2O5/VOSO4前躯体样品的差热和热重分析图。155.73℃、165.54℃和244.33℃三个吸热峰为VOSO4样品分步失水的过程;在300~380℃温度范围内,DSC和TG曲线均无明显变化;当温度达到400℃时,VOSO4开始氧化分解,在580℃以后不再失重。通过理论计算可知,VOSO4氧化分解放出SO2气体失重为32%,与实测值32.28%十分接近,说明567.67℃是VOSO4氧化分解放出SO2气体吸热峰的峰顶温度。此外,根据相关文献[20]可以确定669.91℃是V2O5发生吸热转变的相变温度。因此,可预测在400~580℃范围内煅烧将会得到含有V2O5的VOSO4,并且这一预测可以通过XRD得到进一步证明。

图3-3 V2O5/VOSO4的前躯体TG-DSC曲线
3.2.3.2 红外光谱(FT-IR)
图3-4是干燥后的前驱物在430℃下分别煅烧2h、4h、6h的红外谱图。在500cm-1到1400cm-1范围内,三个样品在939.7cm-1和510.6cm-1附近出现的VOSO4特征吸收峰与文献报道[19]一致,并且峰强度随着煅烧时间的增长而减弱,在1128.5cm-1处的SO不对称伸缩振动峰和400~500cm-1范围内的S
振动峰随着煅烧时间的增长而减弱,后者甚至消失。同时在1018.1cm-1和837.9cm-1附近出现的较强峰分别为V
O振动峰和V—O—V的不对称伸缩峰,这两个特征峰随着煅烧时间的增长而逐渐增强,峰形更尖锐。结合XRD的检测结果,说明延长煅烧时间能促使更多的V2O5生成,VOSO4的量则相应减少。此外,样品在3432cm-1和1624cm-1附近出现了O—H伸缩振动峰和H—O—H的弯曲振动峰,表明2h煅烧产物表面存在少量的吸附水。

图3-4 430℃煅烧不同时间的V2O5/VOSO4红外谱图
3.2.3.3 XRD
图3-5(a)是干燥后的前驱物在不同温度下煅烧6h的XRD图。从图(a)曲线可知,300℃和350℃下煅烧得到的产物没有出现任何物质的衍射峰,而400℃和430℃下煅烧制得的化合物,都出现了VOSO4和V2O5衍射峰,根据两者特征峰的强弱可知,430℃下煅烧产物中V2O5的量比在400℃下煅烧得到的多,而VOSO4的量减少。图3-5(b)是干燥后的前驱物在430℃下分别煅烧2h、4h、6h后的XRD谱图。随着煅烧时间的增长,V2O5的特征峰逐渐增强而VOSO4的特征峰逐渐减弱,对应的V2O5的量增多,VOSO4的量减少。由此可知,随着煅烧温度的增高,煅烧时间的增长,VOSO4逐渐分解为V2O5,导致VOSO4的量减少,而V2O5的量逐渐增多。

图3-5 产物的XRD图
图3-6分别是负载合成V/VOS-Ti-Ba催化剂在430℃煅烧2h、200℃煅烧2h和Co2+-V/VOS-Ti-Ba催化剂在430℃下煅烧6h产物的XRD图。从图中可以看出负载后的催化剂主要成分为硫酸钡,二氧化钛均为锐钛矿相,未检测到VOSO4的峰,只有微弱的V2O5的特征峰。从V2O5的特征峰强弱可以看出,430℃下煅烧6h 的Co2+-V/VOS-Ti-Ba催化剂V2O5的含量较多,同时,该催化剂XRD谱中看不到明显的钴化合物的特征峰,可能原因有两个:一是掺入的钴含量低,XRD未能检测到;二是Ti4+和Co2+离子半径相近(分别为68 pm和72 pm),Co2+完全进入TiO2的结构中,均匀地分散在TiO2晶格中,与之形成了固溶体,导致在纳米复合微粒中检测不到钴元素形成晶体结构的XRD特征峰[21,22]。

图3-6 V/VOS-Ti-Ba和Co2+-V/VOS-Ti-Ba催化剂的XRD图
3.2.3.4 SEM
图3-7中(a)和(b)分别为V/VOS和负载型V/VOS-Ti-Ba催化剂的SEM图。从图中可以看出,两种催化剂的形貌及颗粒尺寸明显不同,其中V/VOS催化剂呈较均匀的片状,颗粒尺寸较大,而负载型催化剂则呈细小颗粒状,颗粒尺寸小得多。可见,负载后的V/VOS-Ti-Ba催化剂颗粒更小,比表面积更大,因此会增大与反应物的接触面积。

图3-7 V/VOS和负载型V/VOS-Ti-Ba催化剂的SEM图
3.2.4 催化剂的催化性能
3.2.4.1 V2O5/VOSO4催化剂的催化活性
现分别以350℃、400℃煅烧6h,430℃煅烧2h、6h和600℃煅烧2h的V/VOS作为催化剂,设置空气流量120mL·min-1,在催化反应温度200~350℃下测试催化剂催化去除o-DCB的活性。表3-3是上述催化剂对o-DCB的催化去除率。从表中数据可知,V/VOS催化剂对o-DCB的催化去除率随煅烧温度的升高、煅烧时间的增长而增大。由XRD结果可知,活性物质V2O5的量随煅烧温度的升高和煅烧时间的增长而增加,因此,催化剂对o-DCB去除活性随着V2O5含量增加而升高。
表3-3 V/VOS催化剂对o-DCB的催化去除率

然而,600℃煅烧2h样品的催化活性却比430℃煅烧6h的稍低些,由DSC-TG可知,600℃煅烧VOSO4完全分解为V2O5,与V/VOS催化剂相比,少了VOSO4充当载体,活性成分得不到很好的分散,不能更充分地和o-DCB接触反应,使得其催化活性下降。因此,可以预测,如果将催化剂负载在表面积大的载体上,可以增大活性成分与反应气的接触面积,催化去除活性可能会更高。
3.2.4.2 负载后V2O5/VOSO4-TiO2-BaSO4催化剂对o-DCB的催化去除
根据V/VOS催化剂对o-DCB的去除结果,选用了200℃煅烧2h的V/VOS-Ti-Ba、430℃下煅烧2h、4h、6h的V/VOS-Ti-Ba,分别在低温200℃和高温350℃考察对o-DCB的去除效果,其他反应条件不变。催化去除结果见表3-4。根据表中数据,在430℃下煅烧的V/VOS-Ti-Ba催化剂在低温和高温下都能催化去除o-DCB,其中高温下去除率达到80%以上,表现出极大的催化活性。而且在该温度下制得的催化剂比在200℃下煅烧的更具有去除活性,说明高温会使VOSO4分解出更多的V2O5,使其在较低的催化温度下就能去除一定的o-DCB。同时,煅烧6h的V/VOS-Ti-Ba催化剂350℃的去除率为97%,而没有负载在TiO2上的V/VOS催化剂在350℃下对o-DCB的去除只有53%,去除率提高了44%,说明负载在二氧化钛上使催化剂活性成分得到更好的分散,添加硫酸钡后,进一步改进了V/VOS-Ti-Ba催化剂的强度和对SOx、HCl的抗性[19],使催化去除活性提高。
表3-4 负载型V/VOS-Ti-Ba系列催化剂对o-DCB的催化去除率

3.2.4.3 不同离子掺杂的V2O5/VOSO4-TiO2-BaSO4催化剂对o-DCB的催化去除
为了进一步提高催化剂的活性、降低催化温度,考察不同离子对V/VOS-Ti-Ba催化剂催化活性的影响。比较掺杂Co2+、Mg2+、Fe3+、Cu2+的催化活性结果发现,掺杂Co2+的活性最高(见表3-5)。
表3-5 掺杂不同离子的催化剂在不同温度下对o-DCB的催化去除率

表3-6是在同一Co2+掺杂量下,考察煅烧温度和煅烧时间对Co2+-V/VOS-Ti-Ba催化剂活性的影响的。从表中数据中可以看出,随着煅烧时间的增长和煅烧温度的升高,其去除率也是逐渐增大的。原因是作用于o-DCB的活性成分是V2O5,其含量是随着煅烧时间的增长和煅烧温度的升高而增多的,所以催化剂去除活性增大。同时,在430℃下煅烧的Co2+-V/VOS-Ti-Ba催化剂比在200℃下煅烧的更具有去除活性,原因可能有两个:一是因为高温下VOSO4分解出更多的V2O5,使催化活性提高;二是和催化剂的颗粒大小有关。Co2+的掺杂使催化活性有了明显的提高,说明Co2+起了正催化效应,原因可能是形成了TiO2-CoO固溶体。根据相关文献[22],掺杂离子进入TiO2晶格并形成稳定固溶体的能力主要取决于掺杂离子的半径和煅烧温度。Ti4+和Co2+的离子半径大小接近,Co2+能够置换TiO2晶体中的Ti4+,形成TiO2-CoO固溶体,而高温煅烧更有助于其生成。固溶体能够抑制TiO2晶粒的长大,使得以TiO2为载体的Co2+-V/VOS-Ti-Ba催化剂有更大的比表面积,能与o-DCB接触得更充分,从而表现出极大的催化活性。并且掺杂Co2+后,当催化温度在300℃时,其催化去除活性已达100%,与没有掺杂的催化剂相比,活性大大提高。
表3-6 Co2+-V/VOS-Ti-Ba系列催化剂对o-DCB的催化去除率

本章采用热分解法制备了以V2O5/VOSO4为主的系列催化剂,通过差示扫描-热重(DSC-TG)、X射线衍射(XRD)、傅里叶红外光谱(FT-IR)、扫描电镜(SEM)等表征手段研究了产物的热分解规律、物相及其形貌,利用固定床催化反应器研究了经不同温度煅烧的产物对邻二氯苯的催化活性。结果发现,V2O5/VOSO4催化剂的催化活性随着V2O5含量的增加而增大。经优化工艺后,制备得到新型负载掺杂Co2+的V2O5-VOSO4/TiO2催化剂,SEM结果表明负载后催化剂颗粒变小,增大了催化剂的比表面积,使之与气相o-DCB接触更充分,提高了催化活性,去除o-DCB的完全氧化温度可降低50℃,具有良好的工业应用前景。