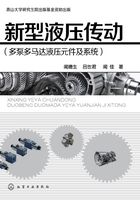
第五节 柱塞底面系统模型
本章以轴向柱塞泵为例,将利用流体传输管道动力学原理,建立柱塞滑靴的管道容腔模型,用空间网格的有限差分方程求解出滑靴底面的流动参量,考虑不同阻尼管尺寸所造成的摩擦阻力项,以及滑靴底面的静压、挤压、热楔导效应,分析静压支承滑靴开路式泵滑靴、CY泵滑靴底面的压力建立过程,以及柱塞与缸体孔摩擦系数,柱塞组质量滑靴密封带尺寸对压力建立的过程影响。
一、模型建立——受力分析
端面配流盘式轴向柱塞泵自1902年问世以来,经过几十年的发展,已经在液压传动与控制系统中得到广泛的应用。近年来,伴随着液压机械向高速、高压、大流量方向的发展,对液压元件,特别是液压系统核心液压泵也提出更高的要求。然而通过对现阶段产品泵,特别是国内外柱塞泵的考察发现,滑靴与斜盘这对摩擦副的摩损已经成了柱塞泵主要的失效形式之一。滑靴的频繁烧损不仅使原先的柱塞泵缸体大轴承寿命作为柱塞泵寿命的评价失去意义,也进一步限制了柱塞泵的应用,在众多需要柱塞泵的场合,不得不以其频繁的更换为代价。所以滑靴与斜盘这对摩擦副的理论研究仍是一件非常有意义的事。
在轴向柱塞泵滑靴与斜盘这对摩擦副的研究方面,国内液压界的学者已经做了大量工作。英国伯明翰大学的C·J·Hooke最早对排量为90mL/r和330mL/r的泵进行了实际工况的油膜测量,证明了滑靴与斜盘之间油膜的存在。图2-72是其测试原理图。即将传感器安在缸体转动的轴向柱塞泵的斜盘上,测出各个滑靴扫过该点时瞬间的油膜厚度。由于未能给出滑靴底面油膜在整个压油区连续变化过程,所以也就不能确定易发生烧靴的区域滑靴底面油膜的具体情况,况且试验中由于仪器的参与,试验结果与实际情况的符合程度也是未知。在他进行本试验以后,又对柱塞泵滑靴的润滑及运行状态进行了一系列的研究,其中有研究滑靴所受离心力和球面摩擦力对运行姿态及润滑影响;滑靴表面的非平面度对滑靴性能的影响;集中负载作用下,剩余压紧力滑靴底面形状与其产生的动压支承力对负载的支承效果;离心力和柱塞滑靴球面摩擦力产生的倾斜力矩对各种形状运行表面滑靴的润滑。总的来说,C·J·Hooke主要研究的是动压支承与滑靴表面形状的关系。

图2-72 四个传感头的位置
日本防卫大学的井星正气等曾在斜盘转动的轴向柱塞泵上实测了静压支承滑靴的油膜厚度,其试验原理为图2-73。他给出了一个转动周期内滑靴底面油膜厚度及压力的变化情况,并从理论上求解了滑靴的运动方程。但他的研究结果也仅适用于低速的斜盘转动的轴向柱塞泵,因为试验时,斜盘转动的柱塞泵相比,柱塞滑靴少了离心力,因此在径向力的分布以及对摩擦力的影响上都有所不同。

图2-73 被试泵结构
1—压力传感器;2—滑靴;3—位移传感器;4—配油阀
1981年,哈尔滨工业大学的许耀铭教授及其研究生韩德才在滑靴模型上进行了油膜厚度及压力的测量,由于测量模型与泵实际工况不同,比如其加载过程可以持续1s到几秒,而实际泵(如25cy型)在额定转速1500r/min的情况下,每个滑靴在压油区只滑行20ms,且受力情况也与滑靴模型完全不同,所以从滑靴模型上测量的压力响应并不能代表实际工况下滑靴底面的压力响应。1988年燕山大学的潘永阁进行了实际工况下滑靴油膜动特性的研究。在理论下他主要采用方向弦阵分析法分析滑靴的运动规律,并考虑了静压、挤压、动压及热楔效应对滑靴的作用。其试验方法是在滑靴上加辅助侧板,如图2-74所示,将滑靴油膜的波动引向回程盘中心,通过测量辅助侧板在回程中心部的轴向运动确定滑靴油膜的厚度。这种方法可以在一定程度上说明滑靴底面油膜的变化情况,但也存在一些固有的缺陷,一方面增加了滑靴的质量,影响了滑靴底面的压力场;另一方面在测量过程中避免引起辅助侧板的振动,造成对测试结果的影响。

图2-74 测试原理及滑靴辅助侧板的安装
1.传输管道动力学理论的发展
为了研究滑靴底面压力的动态响应,就需要精确建立柱塞滑靴的数学模型,因为以往的数学模型都没有考虑柱塞滑靴内部结构的变化,为此本节在柱塞滑靴的建模过程中首次应用了流体传输管道动力学的原理。
流体传输动力学的研究工作最初是为了研究大直径管内流体的瞬态过程,特别是在19世纪末到20世纪初,出于当时水利工程中设计水网分配系统的需要,研究水利工程管系中的水锤现象,应用的方法主要是图解分析法,其理论基础是建立在理想流体无损管路一维波动方程的初级模型上。到20世纪40年代,随着液压技术的发展,管道动力学的研究开始转到小直径管上,由于液压油的黏度比水要大,工作频率比水利系统高,所以研究管道模型中流体惯性和黏性对流体动态过程的影响显得十分重要。黏性主要反映在管道动态流动的摩擦损失,特别是在高频时的频率相关摩擦损失效应惯性主要反映在分布参数的管道流量和压力的振荡。
通过流体管道动力学的研究,可以对管内流体的流动和管道机械进行动态分析,对管道系统进行合理的设计,控制管内非恒定流动,减小管道机械振动,对因机器固有特性或系统正常工作不可避免产生的流体脉动或冲击采取合理的消振和滤波措施,有效地衰减流动脉动和冲击,消除或降低管道振动。
对管内流体非恒定流动的研究主要包括在时域内对管内流体瞬态特性进行分析的瞬态响应和在频域内对管内流体频率特性进行分析的频率响应。一般来说为确定流体管道对与其相连的负载系统的影响。如响应的快速性、稳定性的研究可以采用频域分析;而具体确定管路内的流体在每一时刻、每一位置的流动参数则用时域分析更为合适。特征线法是求解时域系统响应的有效方法。关于特征线理论,早在1948年康伦和弗里特里奇就给出了完整的数学描述,多年来,许多学者都从不同的方面应用这个方法求解稳定和不稳定可压缩流的问题。随着计算机在流体动力学中的应用,综合考虑管路摩擦损耗和传热,使参数可随频率变化的似稳特征线法使计算结果与实际情况更加符合。
对时域内流体瞬态特性的分析主要是应用运动方程和连续性方程得出拟线性的偏微分方程。虽然偏微分方程的一般解是不存在的,但是应用特征线法可以把偏微分方程变成特殊的全微分方程,然后对全微分方程积分,得到便于数值处理的有限差分方程,最后通过计算机求解。这个方法的主要特点是全部求解过程均在时域中进行,而不必涉及由频域到时域的复杂的拉氏反变换问题。
2.滑靴底面静压支承力
对于滑靴底面来讲,N力是由滑靴底面静压支承力、动压支承力、挤压支承力和热楔支承力构成的合力,现分别讨论如下。
(1)静压支承力N静
滑靴底面的静压支承结构如图2-75所示。采用极坐标时,这是一维润滑问题。设在半径r处,取径向宽度为dr,周向夹角为dθ的微元体,设通过该微元体沿径向方向的流量为,则:
(2-137)

图2-75 滑靴底面静压支承结构
式中 h——油膜厚度,mm;
μ——油液黏度。
式(2-137)中的负号是由于流动方向与压力梯度的符号相反而取,则通过半径r圆周的流量Q为:
(2-138)
计算时认为滑靴与斜盘是平行的,所以h和Q不随r值改变。对式(2-138)中的r积分,并代入边界条件:
则压力分布为:
(2-139)
承载能力为压力沿整个表面的积分:
(2-140)
由此可见,当滑靴结构尺寸一定时,静压支承力只与中心油室的压力有关。
(2)挤压支承力N挤
一般认为柱塞刚进入压油区时,滑靴与斜盘之间是存在一定厚度的初始油膜。当作用在柱塞上的轴向力将滑靴压向斜盘时,油膜被挤压变薄,在摩擦副间形成压力场,这种效果称为油膜的挤压效应。挤压效应的存在对减小摩擦副间的摩擦,延长其使用寿命具有重要意义。
由润滑理论雷诺方程的普遍形式有:
(2-141)
在分析挤压过程时,可假定支承面之间无相对滑动,油的黏度为常数,则式(2-141)可写成:
(2-142)
将式(2-142)变成极坐标形式,并假定滑靴无任何倾斜,即和
均为轴对称,则:
由于对称,且h与r无关,则:
(2-143)
对式(2-143)积分,并代入滑靴的压下速度,得:
(2-144)
在分析滑靴的挤压效应时,不考虑其他支承作用,所以可以按圆环的挤压效应(如图2-76)分析。将式(2-144)

图2-76 圆环的挤压效应
代入边界条件:
r=R1时 p=0
r=R2时 p=0
(2-145)
(2-146)
(3)热楔支承力N热
高压油作用在柱塞上,产生的轴向推力将滑靴支承面压向斜盘平面,使滑靴在极薄的油膜上滑行。两滑动面间的泄漏损失和摩擦功率损失都转化成热量,使油膜温度升高而发生容积膨胀,以致产生压力流动,这种在平行间隙间由于热膨胀而产生的承载能力称为热楔支承力。如果不计温度在滑靴表面的分布对黏度的影响,滑靴支承办面上的微元面积Ldy上的热楔支承力可写成:
(2-147)
式中 a0——油液的容积膨胀系数,石油基液压油,a0=(6.3~7.8)×10-4℃-1;
γ0——油液的密度,kg/m3;
C0——油液的比热容,kcal1/(kg·℃);
v——油膜边界的相对速度,m/s;
G——热功当量,G=42700kg·cm/kcal;
g——重力加速度,m/s2。
设支承表面的半径为R',则滑动速度为:
(2-148)
式中,ρ和ωS见式(2-13)和式(2-15)中的ωh。
由图2-77可知,L=R'sinφ,dy=R'sinφdφ,所以滑靴底面总的热楔支承力为:
(2-149a)

图2-77 热楔支承分析
为了减小滑靴与斜盘之间的接触比压,并防止由于压力冲击而引起滑靴底面沉凹的变形(这种变形引起松靴),常常在滑靴的密封带内外加设辅助支承环带,为了不影响滑靴的支承力,辅助支承带的圆周是断开的。
忽略辅助支承上缺损的面积,考虑辅助支承办后总的热楔支承力为:
(2-149b)
(4)动压支承力N动
在不考虑滑靴倾斜时,动压支承力主要由滑靴的密封带、内外辅助支承与它们之间的阶梯结构形成。由图2-78可得压支承力为:
(2-150)

图2-78 阶梯结构动压支承
对应于滑靴的结构,可将其分成如图2-79所示的5个支承区域。辅助支承上的凹形面积,计算时可忽略不计。应用式(2-149b)分别计算各个区域所产生的支承力。
(2-151)
(2-152)
(2-153)
(2-154)

图2-79 滑靴底面动压支承区域
所以 N动=W1+W2+W3+W4+W5
二、柱塞滑靴的设计原理及方法
柱塞组是斜盘式轴向柱塞泵的主要零件,它设计的好坏将直接影响泵的运转及使用寿命。从泵实际损坏情况看,滑靴烧伤、斜盘挂铜是泵主要失效形式之一,一般认为是滑靴与斜盘之间的油膜被破坏而引起金属接触造成的。本节认为造成油膜被破坏的根本原因是滑靴底面支承力不足,使滑靴被压向斜盘,变薄的油膜虽然会使热楔支承力增加,但当它受急剧剪切后会使油温升得过高,油液黏度下降,油膜形成的条件更加恶劣。如果这时油膜厚度与滑动表面的粗糙度和不平度处于同一数量级,就会造成金属接触。从上一节的分析可知,在滑靴底面总支承力中,静压支承力占绝大部分,并且是唯一与滑靴底面压力相联系的力。正确设计静压支承力就是既不能使其过小造成油膜失效,又不能使其过大造成油膜过厚,容积效率下降。通常的设计方法有阻尼管型静压支承法和剩余压紧力法。本节分别给出这两种设计方法,以及由这两种方法设计出的柱塞滑靴结构参数。
1.阻尼管型静压支承设计法
静压支承的概念就是在摩擦副中引入有压油液,使之在一定厚度下产生一个与负载相对抗的力。如果这个力与负载相等,则摩擦副就可以在完全不接触的情况下运动,从而提高效率,减少摩损,延长摩擦副的工作寿命。
要形成静压支承,至少要有一个容腔,使容腔内压力油液通过容腔四周缝隙流动,产生一定的压力分布,如图2-80所示。油腔和节流边内压强产生的力即为承载力。对于结构一定的支承,承载力取决于油腔内的压强。为了使静压支承在变负荷下工作,必须采取措施使二力在允许的油膜厚度下相平衡,办法是在油腔进口前装置阻尼器,使支承具有双重阻尼,即进口阻尼和支承面密封带可变间隙阻尼的串联组合,后者主要控制支承的泄漏量,前者则与后者协同调节油腔压力,当外负载增加,原有平衡被破坏,油膜厚度减小,使通过可变阻尼的泄漏量减小,因为通过固定阻尼的流量与通过可变阻尼的泄漏量是相等的,所以定阻尼器上流量的减小导致压降的减少,油腔内压强增大,承载力增大到与负载重新达到平衡。

图2-80 静压支承示意图
由此可见,由于采取了双重阻尼作用,引起油腔内压强的反馈作用,构成一个自动调节的闭环系统。如图2-81所示,使支承能适合负载的变化。对于圆形阻尼管,其压力-流量特性的表达式为:
(2-155)

图2-81 静压支承方块图
式中 d——阻尼管直径;
l——阻尼管长度;
μ——油的动力黏度;
pr——油腔压力;
ps——供油压力。
可变阻尼的压力-流量特性相当于平行圆盘缝隙流动的情况,即:
(2-156)
式中 h——油膜厚度,mm;
R1,R2——密封带内、外半径,m。
由流量连续性方程可得:
令为支承特性,则有:
(2-157)
式中 k——反映固定阻尼器及支承面间隙阻尼结构形状和尺寸的参数,结构一定时,k为常数。
为了清楚地表达静压支承的工作特性,可将式(2-157)绘成曲线,如图2-82所示。从图中可知k值的变化会引起曲线斜率的变化。

图2-82 静压支承的工作特性曲线
如果将单位油膜厚度所引起的压降系数的变化称为油膜刚度J,则J可表达成:
(2-158)
对式(2-158)微分,可求出最大油膜刚度的条件:
故时油膜刚度最大。
油膜刚度在图2-82中反映的是各曲线的斜率,而处恰好为各曲线的拐点,在这点附近,油膜厚度的微小变化会引起a的显著变化。从理论上讲,这对适应变动的外负载是有利的。
要使静压支承在最佳工况下工作,必须使支承的功率损失最小。静压力支承的功率损失包括泄漏功率损失和摩擦功率损失,泄漏功率损失ΔN1为:
(2-159)
摩擦功率损失ΔN2为:
(2-160)
式中 v——圆盘中心相对于支承面的滑动速度。
由式(2-159)和式(2-160)可知:泄漏功率损失与h3成正比,而摩擦功率损失却与h成反比,因此必然存在一总功率损失为最小的h值,即所谓最佳油膜厚度。
因此最佳油膜厚度为:
(2-161)
在进行阻尼管型静压支承滑靴设计时,只考虑作用在柱塞滑靴上的主要力,即柱塞腔油压引起的压紧力p及滑靴底面上的静压反推力W。计算表明,在稳态时,压紧力p占全部压紧力的85%左右,而反推力W也占全部反推力的85%左右,所以这样设计是可行的。
沿柱塞轴线列平衡方程,有:
即
(2-162)
对于25型轴向柱塞泵,按静压支承设计时,为了保证最大油膜刚度,取稳态支承系数。同时选择斜盘倾角10°为设计工况,由式(2-162)有:
(2-163)
当滑靴尺寸确定后,按式(2-161)计算最佳油膜厚度。考虑到滑靴和斜盘表面的光洁度及平度,油液的滤清度等因素,推荐最佳油膜厚度h=0.01~0.03mm。如果按式(2-161)计算出的h不在此范围内,则h不能作为设计油膜厚度,而要重新选择a或R2/R1进行计算。
为了保证所选定的支承特性a,阻尼管的尺寸必须按设计要求严格保证。由式(2-157)可得:
(2-164)
对照25型轴向柱塞泵柱塞组的结构,取l为25mm,对应不同的R2/R1,由式(2-163)、式(2-164)计算出的柱塞滑靴参数,如表2-8所示。
表2-8 柱塞滑靴参数

不同的密封带尺寸会影响柱塞滑靴的动态特性以及滑靴底面的压力建立过程,其仿真结果分析将在后面给出。
2.剩余压紧力设计法
剩余压紧力法的基本思想是柱塞腔内的高压油无阻尼地通到滑靴底面,使其产生的液压反推力平衡掉大部分柱塞对斜盘的压紧力,而剩余的压紧力则使终压向斜盘而不脱开,靠滑靴与斜盘间形成的边界油膜来减轻摩擦副的摩损。
剩余压紧力法的设计步骤如下。
①根据经验,选取R1+R2=d。其中R1和R2为滑靴底部密封带内、外半径,d为柱塞直径。
②推荐取R2-R1=(0.1~0.15)d,其中直径较大的滑靴取胜较小值,直径较小的滑靴取较大值。
③滑靴底部液压推力为:
柱塞轴向压紧力为:
取压紧系数m为:
(2-165)
压紧系数直接反映了剩余压紧力的大小,决定了滑靴对斜盘的压紧程度,进而决定了滑靴处的摩擦功率损失。因此压紧系数是剩余压紧力滑靴的主要设计参数。
关于m值的选取,国外曾有文献推荐α=0°时,m=1.1~1.12,这样在α=18°~20°时,m将达到1.14~1.17,这种选取将往往导致摩擦副的严重磨损。新的设计思想为α=0°时,m=1,这样在α=18°~20°时,m=1.04~1.05,由式(2-165)计算出的不同R2/R1值的柱塞滑靴参数,如表2-9所示。
表2-9 不同R2/R1值的柱塞滑靴参数

本节所研究的轴向柱塞泵是天津高压泵阀厂生产的确CY和25SPB泵。相当于KZB泵两者柱塞滑靴的尺寸均由剩余压紧力法确定,内、外密封带半径分别为7.1mm和8.9mm。两者的区别在于通油孔的直径。对两种柱塞滑靴的仿真计算及分析将在第五节中讨论。
静压支承设计法和剩余压紧力设计法是两种最基本柱塞滑靴设计方法。本节给出的两种柱塞滑靴参数,为后面进行的滑靴底面压力响应分析及各种参数滑靴动态性能比较打下基础。
三、开闭路式泵滑靴底面动态仿真及试验
在滑靴理论的研究中,有许多研究成果得到了广泛的应用,例如静压支撑设计法、剩余压紧力设计法等。同时在滑靴表面形状上、阻尼槽方式上众多学者也做了大量的研究工作。但由于滑靴底面流体流动状况复杂,研究起来较为困难,并且在实际当中,泵中的相对运动部件不宜安装测试装置,故对泵在实际工作状态下的油膜厚度、压力变化、动态过程等方面的研究较少。通过对闭路式轴向柱塞泵(以CY泵为例)和开路式轴向柱塞泵(以SPB泵为例)进行理论分析、动态仿真和试验比较,可较好地分析滑靴底面压力变化及油膜厚度变化规律。
1.数学模型的建立
为了研究柱塞组在压油区的运动状态,就要建立柱塞组的运动方程。在图2-83所示的坐标系下,假设滑靴向斜盘方向的位移为正,则滑靴挤压油膜的速度为,加速度为
,分别考虑(a)(b)两种情况。

图2-83 柱塞组受力分析及坐标选择
当时,力分解图见图2-83(a),运动方程为:
(2-166)
式中 f——柱塞与柱塞孔的摩擦力,N;
N——斜盘对滑靴的垂直支承力,N;
M——柱塞组的质量,kg;
Fp——高压油对柱塞组的作用力,N;
Fg——柱塞组的轴向惯性力,N;
Fs——回程弹簧对柱塞组的作用力,N;
R——柱塞孔对柱塞的径向压力,N。
当≥0时,N=N静+N热+N挤+N动。
当<0时,N=N静+N热+N动。
当时,力分解图见图2-83(b),运动方程为:
2.特征线理论及在柱塞泵中的应用
为了求解滑靴底面的流动参数,就要建立滑靴底面与柱塞腔相联系的管路——容腔系统,在时域内求解这个系统最方便的办法就是特征曲线法。本节简要描述了特征线理论,求解了圆管内一维非恒定流动,并用特征线法建立了较复杂的柱塞组管路——容腔数学模型。
特征线理论的数学原理:特征线法是偏微分方程的一种数值解法,它将偏微分方程变成特殊的全微分方程,然后对全微分方程积分,得到便于数值处理的有限差分方程。以单变量的一阶拟线性偏微分方程为例进行介绍。
设方程为:
(2-167)
式中 u——因变量;
x,t——自变量。
由于系数a,b,c不仅与x,t有关,还与u有关,所以式(2-167)是拟线性的。求解这个方程的困难之处:在于它包含两个方向(x,t)的导数,但如果能在x,t平面上找到一个方向,使沿这个方向方程(2-167)变为常数微分方面方程来求解就容易多了。式(2-167)可改写为:
若引进方向=
则
(2-168)
由于函数u在此方向上的全微分为:
则式(2-168)可写为:
(2-169)
即偏微分方程(2-167)在沿方向上就变为常微分方程
,沿这个特征方向所确定的特征曲线,对式(2-169)积分就可得沿此特征曲线上u的变化情况。但要注意的是,此时只能给出u沿曲线上的变化情况,而不能给出u在这曲线周围的变化情况,即能沿特征曲线唯一确定u的函数,而不能唯一确定
。
将原方程与全微分方程联立,得到方程组:
(2-170)
由于沿特征方向,不能唯一确定,则方程组[式(2-170)]的系数行列式应为零。
故
此方向为特征方向,沿此方向定出的曲线为特征曲线。又因在特征方向上u是唯一确定的,存在,则:
即
这种引进特征方向,将偏微分方程归结为常微分方程的求解方法称为特征线法。
两个变量的一阶拟线性偏微分方程设方程组为:
(2-171)
式中 aij,bij——x,t,u和v的函数。
采用和前面相同的处理方法,沿特征方向u和v的全微分为:
(2-172)
由方程组(2-171)和方程组(2-172)联立得:
(2-173)
由于沿特征方向及
不能唯一确定,且对应系数的比不相等,所以这些偏导数的系数行列式Δ=0。
令特征方向为,则:
展开后得:
(2-174)
式中
对于式(2-174),显然可知:
①当M2-4HN<0时,k无实根,即无特征方向,方程为椭圆型。
②当M2-4HN=0时,k有一实根,即只有一个特征方向,方程为抛物型。
③当M2-4HN>0时,k有二实根,即存在两个特征方向,方程为双曲线型。
即一阶拟线性双曲型偏微分方程组将存在两族特征方向:
由于沿特征方向函数可能唯一确定,其偏导数存在,因而有Δ1=Δ2=Δ3=Δ4=0。
因为这四个系数行列式是等价的,可以任取,取i=3,则:
展开化简得特征线上的特征关系式为:
(2-175)
式中
这样就将求解含有两个变量的拟线性双曲型偏微分方程问题归结为求(x,t)平面上的两族特征方向以及沿此特征方向成立的特征关系式(kiH+D)du+Edv+Fdt+Gdx=0(i=1,2)的问题。
3.管内非恒定流动基本方程的特征方程和特征关系式
圆管内一维非恒定流动是用平均流速v代表轴向速度,它的数学模型可由动量方程和连续方程求解。在直径为d,截面积为A的管内取厚度为δx的微小流体脱离体,如图2-84所示。压力为p,流体密度为ρ,由动量方程得:
(2-176)

图2-84 动量方程隔离体
式中 下标x——该参量对x的偏导,在因变量上加一个圆点代表该量对时间的全导数;
α——管子与水平线的夹角,当高度沿正x方向增加时α为正,在这里,舍去高阶的δx量,并设管道水平放置(α=0),则式(2-176)可写为:
(2-177)
式中 τ0πd——一项与流量有关的摩擦阻力项,在这里记作f(Q),f(Q)值的计算将在后面讨论。
因为
代入式(2-177)中得:
(2-178)
方程式(2-178)中有两个变量,求解还需建立另一个方程。
在圆管内取长度为δx的控制体,如图2-85所示。考虑到在动态情况下,管壁将有u的运动速度,由连续性原理可知:

图2-85 连续性方程用控制体
由此得:
(2-179)
因为
代入式(2-179)得:
由此得
或
(2-180)
由于流体的弹性模量Ke为:
而
(2-181)
(2-182)
式中 /A——面积相对膨胀率;
E——管材的弹性模量,Pa;
μ——管材的泊桑比;
D——管道外直径,m;
b——管壁厚度,m。
将式(2-181)和式(2-182)代入式(2-180)中得:
考虑管壁变形时的压力波传递速度a为:
(2-183)
所以式(2-183)又可写成:
(2-184)
式(2-178)和式(2-184)即为管内非恒定流的基本方程,又称波动方程。因为在一般的流体管道中,有a≫v,因此式(2-178)和式(2-184)中的第二项均可舍去,波动方程可写为:
(2-185)
用上节的特征线法将式(2-178)和式(2-184)改写为:
(2-186)
将方程组(2-186)与式(2-171)相比较,对应得出u=p;a22=ρ/A;a11=1;a12=0;g1=0;a21=0;a22=ρ/A;b21=1;g2=-f(Q)。
由此可以算得;
;
;
;
。
所以
(2-187)
式中 v——管内流体流速,m/s;
a——压力波传递速度,且v≪a,m/s。
所以求得两个特征方向为:
(2-188)
将系数H、D、E、F、G以及无阻尼特征阻抗Z0=ρa/A代入式(2-175)中并整理得
(2-189)
最后得到波动方程经特征线解法变换的四个常微分方程:
(2-190)
4.用空间网格插值法数值求解波动方程
为了数值求解波动方程,就需要用正交网格来离散它。将一根管道分为n份,每段长度Δx≥αΔt,在图2-86的矩形网格中取Δt=Δx/α。其求解的基本思想是根据前一时刻各网格点上已知的流动状态参量p和q,利用离散化的特征方程和特征关系式去求得下一时刻各网格上的流动参量p和q之值。

图2-86 特征线网格
对波动方程中,式(2-178)、式(2-184)分别乘上dt并积分,最后整理得:
(2-191)
(2-192)
采用空间网格差值时,为了减少数值误差,可能采用通过增加管道分段数和控制网格比Bs的办法。具体地说,管道分段数越多,误差越小。网格比Bs也要尽量接近于1,通常可取0.85≤Bs≤0.98,对于多管路系统,应使各管路有共同的时间步长和分段长度。而Δt和Δx的选择还应在计算机认可的范围以内。
5.流体管道黏性摩擦损失的计算
高黏度性质的流体在管内做非恒定流动时,其剪切摩擦损失具有频率相关的特性,其黏性摩擦损失为:
(2-193)
经整理的差分方程:
(2-194)
在用特征线法计算左右特征项时,由于f[q(t+Δt)]为未知量而无法直接计算出CL和CR,这时可以对未知f[q(t+Δt)]进行一次迭代,黏性摩擦项作估算,并求出估计的q'(t+Δt),然后代入原式计算。
6.柱塞滑靴组的管道动力学模型
为了保证轴向柱塞泵的正常运转,就要使滑靴与斜盘这对摩擦副间始终存在一层润滑油膜,这层油膜的油就是从缸体的柱塞腔经柱塞与滑靴中的通油孔引到滑靴下面。虽然这层油膜的厚度是受柱塞与滑靴两端力的共同作用,但通油孔(即管道)的形状却直接影响滑靴底面的流动参量,如压力和流量。所以建立柱塞滑靴组的管道动力学模型对分析柱塞组的运动状态,了解滑靴底面压力建立过程是很有必要的。从结构上看,无论是CY泵,还是SPB泵,其柱塞组都可以看成是由管道和容腔组成的系统,如图2-87所示。

图2-87 柱塞组管道容腔模型
1—柱塞腔;2—管道1;3—管道2;4—容腔
经推导和计算可得流体状态方程:
(2-195)
式中 p——容腔内的压力;
qj(p)——第j个管道或元件流入容腔的流量(j=1,2,…,n),定义流入容腔的流量为正,流出容腔的流量为负。
高滑靴下压速度为v,对式(2-195)一阶线性逼近,则有:
(2-196)
式中 1、i——前后两时刻;
CL2——管道2的左特征值,且保证每一时刻,管道2的终端压力均与空腔内压力相等;
R3,R4——滑靴密封带半径;
h——油膜厚度;
x0——管道2的特征阻抗。
在式(2-196)中,右式第一项为单位时间因滑靴下压引起的容腔体积变化;第二项为单位时间从管道2进入容腔3的容积;第三项为通过滑靴密封带漏出的流量。
经过推导,建立用特征线法求解的管道-容腔模型,联立柱塞组的运动方程式,即可求解滑靴底面任意的流动参数和运动参数。
7.柱塞滑靴组动态仿真
(1)程序框图
前面已经全面分析了与柱塞组有关的运动参数和流动参数,给出了运动方程和流体的传输方程。由于将两个方程耦合所得到的方程是非线性的,数学上解析求解是很困难的,为此在Vax780上进行了数值求解,程序框图见图2-88。

图2-88 仿真程序框图
(2)滑靴底面流体参数的仿真
用本节建立的柱塞滑靴仿真模型,可以很方便地求解滑靴底面的流动参数。针对不同的配流盘形式,将柱塞腔压力分别按拟斜坡信号和阶跃信号输入模型。
①柱塞腔压力的拟斜坡信号输入 由于试验条件所限,本节的试验只能在压力小于8MPa的试验台上进行,所以在理论上重点研究了6MPa压力下,滑靴结构参数和柱塞组运动参数对滑靴底面流动参数的影响。
a. CY泵柱塞组参数。阻尼孔直径1.5mm,质量0.1kg,摩擦系数0.05。SPB泵柱塞组参数:阻尼孔直径4mm,质量0.095kg,摩擦系数0.05。两滑靴底面完全相同。由图2-89和图2-90可知,在压油区,滑靴地面的压力和油膜厚度并不是一个恒定的值,而是在以很高的频率振荡,压力的波峰与波谷分别对应油膜的波峰与波谷。大阻尼孔的滑靴,压力响应频率快,压力幅值在20~100bar之间,油膜平均厚度在17μm左右;小阻尼孔滑靴压力响应频率慢,压力幅值在30~110bar之间,油膜平均厚度12μm。

图2-89 SPB泵滑靴底面压力与油膜厚度曲线
b.考虑压力传感器影响。在压油区40~420加入传感器容腔,仿真曲线见图2-92、图2-93。与图2-90和图2-91相比,滑靴在接触传感器容腔的瞬间,压力被缓冲释放,所以压力振荡幅度比较大,而容腔增大使振荡频率降低。与CY泵滑靴相比,SPB泵滑靴由于阻尼作用相对较小,压力响应频率高,油膜可以维持在比较高的水平。

图2-90 CY泵滑靴底面压力与油膜厚度曲线

图2-91 考虑容腔效应的SPB泵滑靴底面压力与油膜曲线
c.考虑柱塞与缸体柱塞孔不同摩擦系数的影响见图2-91、图2-92。柱塞在缸体柱塞孔中往复运动,随着工作时间的增加,由于摩损以及油液中杂质的影响,摩擦系数会有所改变。仿真时在前述a.参数的基础上,将摩擦系数增大到0.12。从曲线上看,两种滑靴底面压力更加不规则,平均油膜厚度均有下降。但粗阻尼孔的滑靴仍表现出比细阻尼孔的滑靴更好的性能,即压力响应频率高,在同样的油膜厚度下,压力振荡幅度小,在压油区平均厚度高。

图2-92 考虑容腔效应的CY泵滑靴底面压力与油膜曲线
d.剩余压紧力法设计的滑靴,其底面的压力与油膜曲线见图2-93、图2-94。CY泵滑靴和SPB泵滑靴都是用剩余压紧力法设计的,相比之下,SPB泵滑靴底面压力和油膜振荡的幅度比较大,平均油膜厚度在25μm左右。CY泵滑靴底面平均油膜为10~14mm。CY泵与SPB泵滑靴密封带尺寸比为1∶1.25,而压力和油膜厚度都要高于静压支承法设计的滑靴。

图2-93 摩擦增大后粗阻尼孔滑靴底面压力与油膜曲线

图2-94 摩擦增大后细阻尼孔滑靴底面压力与油膜曲线
②柱塞腔压力的阶跃信号输入 以往在研究柱塞泵其他方向问题的时候,为了方便起见,将柱塞腔压力视为标准的方波信号,利用本节的仿真模型,可以很方便地看出这种简化对滑靴底面压力与油的影响。
a. 6MPa时滑靴底面流体参数曲线由图2-95和图2-96可以看出,两滑靴除了幅值以外的响应过程是极为相似的。这是因为两滑靴都是用剩余压紧力法设计的。

图2-95 CY泵工作压力320bar时滑靴地面压力与油膜曲线

图2-96 SPB泵工作压力320bar时滑靴地面压力与油膜曲线
b.对于6MPa的阶跃输入,滑靴底面压力信号可以近似地看成二阶系统的响应。SPB泵柱塞组与CY泵柱塞组相比,超调量大,过渡时间短,所以它的阻尼比小,无阻尼自振频率高。对柱塞腔内压力在大油区的脉动,SPB泵滑靴都有较高的响应频率,使滑靴底面压力与油膜适应柱塞腔压力的变化。这一点从图2-89和图2-90也同样可以看出。
考虑传感器容腔的影响,将图2-91、图2-92中的传感器容腔用在柱塞腔压力阶跃输入状态,得到图2-97、图2-98。

图2-97 CY泵6MPa阶跃输入滑靴底面压力与油膜曲线

图2-98 SPB泵6MPa阶跃输入滑靴底面压力与油膜曲线
SPB泵滑靴底面容腔突然改变时,其压力过渡时间短,压力幅值高,油膜比较厚。这与(1)得出的结论是一致的,见图2-99、图2-100。

图2-99 容腔效应阶跃输入CY泵滑靴底面压力与油膜曲线

图2-100 容腔效应阶跃输入SPB泵滑靴底面压力与油膜曲线
8.试验方法及结果分析
由于柱塞泵内部结构紧凑,所以在其内部安装测量装置一直是比较困难的,特别是缸体转动的斜盘式柱塞泵,几乎不可能在结构紧凑且又不断运动的滑靴上测出滑靴底面流动参数的连续变化。针对这一情况,试验采取在斜盘的同一位置测量不同泵的滑靴底面压力的办法。具体地说,对转速相同的泵,滑靴从进入压油区到经过斜盘上某一确定点的时间是相同的,而对应相同的配流盘形式,柱塞腔内压力给定状态也是相同的,这样同一台泵上测量不同滑靴所得到的结果就具有可比性。试验时由于测量仪器的参与,滑靴底面的容腔将被改变,计算表明,传感器的容腔体积是滑靴底面的压力将被全部释放,所以,在测量点上就人为地造成一个压力建立过程。分析这个压力建立过程,同样可以说明不同结构的柱塞滑靴其底面压力的响应过程。图2-101为试验原理图。由于试验,需要加工的零件有定量斜盘(图2-102)和定量端盖(图2-103)。

图2-101 实验装置示意图

图2-102 定量斜盘

图2-103 定量端盖
试验结果与仿真结果的对比分析:试验是在伺服泵站的试验台上进行的。由于试验设备的限制,最大工作压力只能升到8MPa左右,所以测量时的调定压力均小于8MPa。测量得到的滑靴底面压力信号用示波器显示并用胶片记录,记录的曲线见图2-104、图2-105。

图2-104 SPB泵6MPa

图2-105 CY泵6MPa
CY泵与SPB泵试验曲线上幅值的差异是由于两次测量时示波器幅值增益调定不同。另外在测量CY泵滑靴底面压力时,电信号受到干扰,所以使波形受到一定影响。信号的幅值同电压表标定结果见表2-10。
表2-10 信号的幅值同电压表标定结果

①对比两种滑靴试验曲线,可以看出用剩余压紧力法设计的两滑靴,压力建立过程是很相似的。由于接入压力传感器的容腔,滑靴底面压力被释放,柱塞组原有的动态平衡被打破,压力重新建立,在信号的初始端有一些振荡,这一点同仿真结果是一致的,同时也说明仿真结果的可信度是比较高的。
②从考虑传感器容腔的仿真曲线看,在测压区间后半段(即2.5~5ms之间),压力逐渐接近柱塞腔压力6MPa,而图2-104、图2-105的试验值为5MPa。这是因为在试验中,测试点虽然开在压油区27°处,但传感器测到的却是滑靴内密封滑过测试点的一个动态过程,在示波器上可以给出压力的动态变化,但在用于静态测量的电压表上测出的却是包含滑靴之间间隔的一个静态平均值,这也是试验值与仿真结果存在一定差异的原因。
③柱塞腔内压力的瞬态变化对滑靴底面压力建立过程有很大影响。试验所用的柱塞泵为进出口可变的双向柱塞泵,配流盘采用的是双向设计的减振孔形阻尼结构。分析表2-10的结果可以得出:在3MPa泵输出压力下,滑靴底面压力受压力超调的影响是比较大的。而在6MPa时,仿真研究中柱塞腔压力分别以无阻尼结构的阶跃信号和有阻尼的无冲击拟斜坡信号输入,试验结果表明,仿真模型所得到的结论与试验曲线是比较一致的。
9.结论
通过对滑靴底面流体参数的理论分析和试验研究,得出以下结论。
①柱塞滑靴在压油区始终处于动态平衡状态,滑靴底面的压力和油膜厚度也不是恒定不变的,而是以很高的频率振荡,振幅及振荡频率取决于柱塞组的阻尼孔及滑靴密封带尺寸。在柱塞组结构一定时,滑靴底面压力与油膜厚度有直接关系。压力高,对应的油膜就比较厚。
②影响滑靴底面的流体参数主要有阻尼孔径和密封带尺寸。阻尼孔径大,压力响应频率就比较高,油膜平均厚度大。密封带尺寸比不宜太小,最小不应小于1.2。
③滑靴底面压力受柱塞腔内压力的影响比较大。试验所得压力曲线介于阶跃信号和斜坡信号输入的仿真结果之间,如果能将柱塞腔压力的试验值采样记录下来作为仿真研究的输入,会使理论与实际更加符合。
④从仿真结果看,静压支承滑靴为了保证支承特性,必须减小阻尼孔径,由于阻尼作用很大,压力与油膜振荡的幅度很小,油膜厚度也比较低;剩余压紧力滑靴,阻尼孔径的选择不必考虑支承特性,所以压力响应频率高,平均油膜往往是静压支承滑靴的1~2倍。