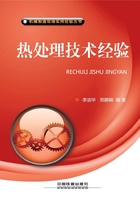
4.金属热处理前后如何进行清洗?
清洗是指清除工件表面的液体和固体污染物,使工件表面达到一定的洁净度的工序。清洗也是热处理生产过程中不可忽视的中间辅助工序。所有经机加、热处理前的工件都应进行清洗。否则,热处理前、后工件表面上的油污进入炉内加热挥发和燃烧,容易造成车间空气污染,影响工件表面状态,甚至影响工件的热处理质量。对化学热处理以及真空热处理而言,工件的清洗可以提高热处理生产效率及热处理质量。
清洗过程是清洗介质、污染物及工件表面三者之间的相互作用,是一种复杂的物理与化学作用的过程。清洗不仅与污染物的性质、种类、形态以及粘附的程度有关,与清洗介质的理化性质、清洗性能、工件表面状态有关,而且还与清洗时的条件有关。如,温度、压力以及附加的超声振动、机械外力等因素都会影响清洗效果。
清洗热处理前后工件表面污染物的方式很多,有浸渍清洗、喷气清洗、喷流清洗、喷淋清洗、减压清洗、喷雾清洗等。使用时可以根据污染物类型和要求的清洁度来选择合适的清洗方式方法和设备。
为了保证零件的清洗质量,清洗者还要严格控制清洗工艺要素。例如,要了解热处理前道工序和前道工序在工件表面形成的污迹;根据污物类型选择清洗剂,确认其清洗能力和污物被完全清除的可能性;预测水的质量,如水的硬度过高,还要考虑采取软化水的措施;掌握清洗剂的生物稳定性,以防生长细菌和真菌;应尽量避免使用杀菌剂和防霉剂;清洗剂工件表面残留物不应在回火时形成烟雾,不应使工件表面生锈,不应使工件变色;清洗工件应合理码放,喷嘴相对于工件的位置要合适。因此,清洗前了解工件表面脏物的类型、清洗剂的使用范围、清洗方式很重要。
(1)工件表面脏物的类型
工件表面脏物种类是选择清洗剂的重要依据,也是确定清洗条件的重要出发点。工件表面脏物大致可分为六类。
1)带颜色的拔丝化学物质。金属拉延、拔丝会发热,促使颜料进入金属表面孔隙,给清洗造成困难。采用超声、电解和高压喷射清洗有助于除去这些化合物。
2)不带颜料的拉延化学物质。通常用热碱液可除掉这些物质。如遇到高黏度脏物,则需在溶剂或乳化剂中进行预清洗,以溶解部分脏物和减少其黏度,以使随后的碱液清洗更好发挥作用。
3)机加工切削液。用合成清洗剂和碱性清洗剂能轻易除去可溶性油、合成切削液和乳化切削液。用碱性清洗剂难于除去含硫和含氯化合物,有时必须用溶剂或乳化溶剂。含脂肪酸的切削液容易和碱性清洗剂反应,获得好的清洗效果。
4)抛磨膏。抛磨时会发热,零件表面附着的抛磨膏难以去除。要避免抛磨膏老化和过度抛磨。老化引起聚合反应,而过度抛磨会在工件上留下大量膏剂。通常要使用高清洗力和溶解力清洗剂。
5)碳质脏物。干燥细碳粒是比较难去除的脏物,须采取高压喷射等措施。用乳化清洗剂加超声波经常有好的效果。
6)锈蚀、氧化皮和油漆。除这些脏物需采取特殊措施。轻度锈蚀和硝基漆可用苛性碱清洗剂。重度氧化皮必须用酸。除铝和锌金属上的漆必须添加洗漆剂。
除以上污物外,还有一些特殊的因素和污物性质需要考虑。如,污物的物理性质,包括污物的液态黏度和熔点。对于污物中的一些极细微粒,应提前采取特殊措施去除。对于污物中的腐蚀氧化产物,应采取适当中和方式,以避免伤害工件。
(2)清洗剂
清洗剂依其化学性质可分为碱性清洗剂、酸性清洗剂、合成清洗剂、可溶性乳化清洗剂和去污剂等。
碱性清洗剂。碱性清洗剂是一种使用最广的清洗剂,由增洁剂和表面活性剂的碱土金属盐混合配制而成。添加每一种盐和表面活性剂的出发点一是保证清洗效果,二是经济性。要求清洗剂的pH值保持在7左右。此类清洗剂的增洁成分是氢氧化物、硅酸盐、磷酸盐、碳酸盐、硼酸盐以及有机螯和物。
氢氧化物可提供较高的碱性,相对低廉,少量添加即可提供溶液所需的碱性和导电性,这对于电解清洗和皂化非常重要。其缺点是较难漂洗,脏物的非皂化清洗效果不良。1%浓度溶液的pH值即可达13。碱性清洗液可用钠盐,也可用钾盐,主要用于铁基合金的清洗。
硅酸盐是可以配制在苛刻条件下使用的碱性清洗剂。原硅酸钠、硅酸钠都是优异的促进乳化剂。在pH值>9时是很好的缓冲剂,能使污物存留在悬浮液中获得高的碱性度。硅酸钠是金属清洗剂中常用的硅酸盐。在碱性清洗剂中加入这种物质可缓和清洗剂对铝和锌的侵蚀。在电解清洗过程中,硅酸盐会在钢件表面留下黑色锈斑。为提高清洗剂的多用性,各种碱性清洗剂都含有硅酸盐。在对基体金属无侵蚀或少量侵蚀前提下可提供高的碱性度(PH值较高)。浓度为1%的硅酸盐溶液的pH值可达到12.3。
磷酸盐在金属清洗剂中具有软化水的功能,可提供碱性度和使污物胶溶,使大的粒子粉碎成小粒子。因为有些国家和地区禁用磷酸盐。因此,有人采用有机螯合物对镁和钙离子以及多种重金属离子实行多价螯和,用来作低、中等碱度范围复合磷酸盐的代用品。
碳酸盐是碱性度的低成本来源,也可在一定程度上软化水,属弱清洗剂,可提供中等碱性度,在金属清洗剂中的主要作用是有助于获得高流动性、无黏性的混合液。在碳酸盐中使用最广的是碳酸钠或苏打粉。因为价格低廉,几乎在所有配方中都或多或少含的有碳酸钠。浓度1%的碳酸钠溶液的pH值可达11.3。
硼酸盐用于低pH范围可防锈的清洗剂。在1%溶液中加入10mL硼砂,其pH值为9.2。硫酸盐可用作填充剂,但也有人愿意采用碳酸钠。
碱性清洗剂含增洁剂和表面活性剂。只用增洁剂不能获得理想去污效果,必须结合使用表面活性剂。由于表面活性剂含有两种分离组分,一组溶于油,另一组溶于水,它具有在表面聚集的性能,有渗入表面能力,可防止污物再沉积,并降低溶剂的表面张力。碱性清洗剂用的表面活性剂有非离子型、阴离子型和阳离子型三种。
非离子型表面活性剂由于其多功能被广泛应用。在不同非离子表面活性剂中施行优选可获得最强的净化能力、最大的油溶性和最大的消泡能力。
阴离子型表面活性剂、带负电的分子微粒是最大和最重要因素,除去油脂特别有效。通常在配方中把非离子型和阴离子型结合起来使用。
阳离子型表面活性剂带正电的组分是最多和最重要的。阳离子性清洗剂是弱清洗剂,通常用作杀菌剂和纤维软化剂。
酸性清洗剂。酸性清洗剂对于清除金属制件上的氧化皮等特殊附着物十分有效,最有名的工艺是酸浸。除轧制、焊接和热处理氧化层,影响电镀、油潦质量的表面氧化物、生锈和腐蚀产物以及硬水沉积物都可用酸去除;通常使用的有硫酸、盐酸、磷酸、硝酸和柠檬酸、醋酸等有机酸。当前使用的主要是前三种。酸性剂含有基础酸和防止侵蚀金属表面的缓蚀剂以及提高清除能力的表面活性剂。
合成清洗剂也是一种按pH值区分的碱性清洗剂,但和标准碱性清洗剂有所不同,区别在于化学成分。标准碱性清洗剂实质上是无机的,而合成剂则是含胺基物质的有机用剂。这类产品被设计用来清除单段清洗中的碱性残留物,而且还是好的防锈剂。合成清洗剂被用来进行中等难度的清洗,如清除工件表面的淬火油和聚合物溶液。
可溶性乳化清洗剂。可溶性乳化剂通常含有泥土、溶剂、乳化剂、增洁剂、缓蚀剂和少量水。水的作用是使乳化剂溶解。该清洗剂除可溶解工件表面污物,还可在表面留下防锈膜。其中的乳化剂和洗涤剂能抓牢油脂微粒,并将其溶入含有溶剂和油的清洗剂中。乳化清洗剂是一种浓缩态的纯油产品,将其在水中稀释后便成为白色乳状液体。
去污剂。去污清洁剂主要含有溶剂、表面活性剂和水,不同于乳化清洗剂,是纯溶液,不是乳化液。他们主要用作地板、机器、墙壁等的维护性清理。
对于清洗剂的选择,使用者可根据污物种类和采用的清洗工艺(喷射、浸洗、超声等)选取合适的清洗剂。碱性清洗剂用来清除带腐蚀性脏物。中性清洗剂用在有缓蚀要求和清除缓和性能的污物。淬火油通常被认为是缓和污物,除非其性能被严重恶化。
乳化清洗剂的选用通常取决于下道工序,含防锈剂的油膜随后能保留在工件上。要求特别清洁的零件可选用溶剂清洗剂。出于对环境影响,氟氯烃等溶剂的使用越来越少,但特别清洁要求的零件又在不断增多,人们正在努力寻求既不影响环境,又能满足高清洗质量要求的无公害溶剂。
(3)清洗方式与方法
热处理行业的清洗环节主要有两个:一是热处理前的清洗,主要是清洗前道工序残留的切削油、切削液及防锈油等附着物;二是热处理后清洗,主要是清洗淬火后的残留淬火油。按照清洗方法和原理可分为:物理清洗、化学清洗等。
物理清洗。物理清洗是指借助各种机械外力和能量使污垢粉碎、分解并剥离物体表面,从而达到清洗效果。常用的方法有喷淋、高压水射流、搅动、超声波清洗等。
化学清洗。化学清洗是指采用一种或几种化学药剂(或其水溶液),借助清洗剂对物体表面污染物进行化学转化、溶解、剥离并达到清洗效果。
清洗方式分为浸渍清洗、喷气清洗、喷流清洗、喷淋清洗、减压清洗、喷雾清洗。
浸渍清洗是将工件放在清洗槽中进行清洗。槽中加入清洗液,将被洗物浸渍其中的清洗方式。由于仅靠清洗液的化学作用清洗,所以洗涤能力弱,需要长时间。
喷气清洗,在清洗槽内安装喷气喷管,用气体将清洗液喷射到被清洗工件上的清洗方式,压力>2MPa。
喷流清洗,从槽的侧面将清洗液在液相中喷出,靠清洗液的搅拌力(物理作用)促进洗涤。洗涤能力比浸渍清洗强。
喷淋清洗,在清洗槽内安装喷淋装置,将清洗液喷射到被清洗工件表面,清洗压力<0.2MPa。
减压清洗,在清洗槽内产生负压,由于减压,洗涤剂能较好地渗透到被洗物的缝隙之间。若和超声波配合,清洗效果会大大增加。
喷雾清洗,在清洗槽内安装喷雾管,在气相中将洗涤剂喷附到被清洗零件上的清洗方式。压力一般为0.2~2MPa。
零件的清洗要达到一定的清洁度,要达到何种清洁度取决于客户要求和随后的加工工艺。