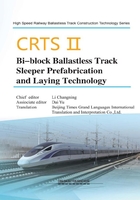
2.7 Sleeper Construction
2.7.1 Rebar processing
The supporting structure is welded by upper chord rebar N1(12),lower cord rebar N2(2×10)and wave rebar N3(2×6),usually welded by means of mechanical resistance spot welding method,the yield shear stress for each welding point shall not be less than 8 kN.
The bent rebar and mesh rebar shall be welded on special clamping apparatus,the welded reinforcement cage and the truss bars shall also welded on the special clamping apparatus,with size and quality meeting the design requirement.
The rebar cutting machine and rebar bending machine shall be used for processing of semi-finished rebar.The rebar material shall be prepared by the rebar cutting machine,the rebar after cutting shall be stacked and marked according to different serial numbers.
The truss bar forming machine shall be used for processing truss bars.The truss processing can be parallel with other working procedures,but the other working procedures can be operated earlier to ensure certain reserve of scattered rebar parts.The welding for rebar mesh and truss rebar shall be sampled inspection for each shift,to check whether the truss rebar is twisted and whether there is welding failure or cold solder for every welding point.When automatic equipment are applied for production,material feeding,aligning,cutting,bending and welding forming,etc.,the efficiency shall be focused upon under the premise that the size of all parts satisfy the requirement.
Table 4 Allowable Size Deviation for Rebar Processing Forming

2.7.2 Formwork cleaning
After the sleeper is formwork removal,the formwork shall be delivered to the formwork cleaning work position,then formwork cleaning worker shall use special tools(like polishing machine,sand cloth and scraping knife,etc.)to clean the attachment such as concrete residue and stickum,especially the locating position like the rail bearing platform for the formwork and embedded sleeves,and the concrete shall be particularly cleared away inside the reserved groove for truss rebar at the bottom of the formwork.Afterwards,the cotton cloth shall be used to clean the residue inside the formwork,to ensure the formwork surface cleaning.The quality inspection personnel shall visually check the polishing effect,or touch with their fingers inside the basin to check the formwork degree of finish.Figure 10 shows the formwork polishing and cleaning.
The formwork shall be checked whether it is broken,whether it is smooth inside,whether the surface is smooth,whether there is concave convex phenomenon,whether there is any deeper scratching which may influence sleeper surface smoothness,and whether the marks and signs are broken or transformed.If such phenomena occur,the formwork shall be lifted out of the roll table to repair or replace.
2.7.3 Formwork releasing agent spraying
The quality control point for spraying formwork releasing agent:the formwork releasing agent shall be sprayed before installation of embedded sleeves,to prevent the sleeve surface from being pasted with the agent.The formwork releasing agent shall be sprayed appropriately,and shall not be accumulated inside the formwork.Inside the formwork shall be completely sprayed with the formwork releasing agent,the edges of the formwork in particular,otherwise the sleeper edges may easily be broken in formwork removal,and the formwork removal effect and the smoothness of the sleeper surface will be influenced.

Figure 10 Formwork Polishing and Cleaning
2.7.4 Embedded sleeve and spiral bar installation
The specific installation steps for embedded sleeve installation:the firmness of the locating pin shall be checked for the embedded sleeve at bottom formwork,fasten it if necessary and make it vertical to bottom formwork,then the sleeve shall be fastened on the locating pin with self-made installation tool.The sleeve shall be checked whether it is vertical with the bottom formwork,the sleeve shall be removed if necessary and shall be installed again after the locating pin is checked and cleaned.Figure 11 below shows the actual installation case for sleeve and spiral bar.

Figure 11 Sleeve and Spiral Bar Installation
The installation quality for sleeves shall be inspected one after another,mainly on whether every embedded sleeve is closely attached to the bottom formwork,whether the embedded sleeve is loosened after rotating test,and whether there is gap between the embedded sleeves and the bottom formwork(the testing device like feeler gauge shall be used,gap is not allowed).The spiral bar shall be installed and oriented on the embedded sleeve upon all the inspection items are qualified.The screw thread of the sleeve locating shaft shall be periodically checked,and shall be replaced immediately if the screw thread is broken.
The spiral bar of the embedded sleeve adopts ϕ 4 mm low carbon cold drawn wire,whose technical requirement shall meet that of Low Carbon Steel Wire for General Purpose(YB/T 5294-2009).The rebar of this model is variable diameter spiral rebar,if consigned processing shall be under site inspection strictly based on drawings,and the defected products shall not be accepted.
2.7.5 Rebar truss into formwork
Upon completion of embedded sleeve installation,the formwork shall be delivered to the work position for rebar truss installation,into which the construction personnel shall lift up the reinforcement cage.The reinforcement cage shall not touch the embedded sleeve while it is moving into the formwork.The reinforcement cage shall be adjusted immediately if it is deflected or twisted.The guiding rule shall be used on site with vertical sides placed on the side formwork at both sides,the steel rule shall be used to measure the distance between the bottom edge of the guiding rule and the upper edge of the rebar,and the position shall be adjusted for the reinforcement cage along sleeper depth.
2.7.6 Mortar blocking plate installation
The mortar blocking plate shall be securely installed,with correct position,without loosening or leaking phenomena.The mortar blocking plate shall be installed before concrete pouring and vibration on the concrete roll table.
The single mortar blocking plate shall be integrally designed and produced under the premise that they can fix 4 upper cord rebars of the 2 neighboring sleepers.The mortar blocking plate will have to ensure the truss bar not inclining and floating in the formwork.
2.7.7 Concrete batching and pouring
1.The mixture ratio for sleeper concrete shall be designed according to the requirement of Temporary Technical Condition for High Performance Concrete of Passenger Dedicated Railway,the basis mixture ratio which meet the design and construction requirements shall be selected,the durability indexes(freeze-thaw resistance cycle performance,chloride resistance electric flux,crack resistance and alkali-resistant aggregate reaction performance)shall be inspected to ensure their conformation to specification requirement,the basic mixture ratio of C60 concrete shall be finally determined,as is shown in Table 5.
Table 5 Concrete Mixture Ratio for Bi-block Sleeper(Consumption of Every Cubic Material)

2.The batching for concrete mixing material is measured by automatic metering device,the water content of coarse and fine aggregate shall be tested in time,the water content and consumption of coarse and fine aggregate shall be determined by the actual testing values,and the construction mixture ratio can finally be decided.The sequence of raw material charging is sand and cement → admixture and water → broken stone.
3.For construction in hot seasons,the cement temperature shall be controlled not higher than 40℃before charging into the mixer,and the temperature of concrete batching material shall be lowered so as to ensure the concrete temperature meeting the requirement for formwork entering.When the average temperature of day-night is lower than 5℃for 5 days on end or the lowest temperature is lower than -3℃,the concrete batching process for winter season shall be applied,the concrete mixture ratio and slumps shall be strictly controlled,and anti-freezing insulation measures shall be taken to ensure the concrete quality.When ambient temperature is within -5~5℃,the water for bathing shall be heated to 40~60℃before mixing.When the ambient temperature is below -5℃,the water for batching shall be heated to 60~80℃.The water shall be heated while being charged in concrete batching process.The sequence for material charging in concrete batching is sand → stone → hot water → cement → admixture.The sand-gravel aggregate and water shall be charged into the mixer and mixed evenly,which can play the role of heating the aggregate; the admixture shall be transported into the warm shed for natural heating,direct heating is prohibited.Since the hot batching process is adopted,the batching time shall be prolonged to 0.5 min(original batching time 3 min),which can effectively guarantee the concrete workability.
2.7.8 Mortar blocking plate removal
The mortar blocking plate shall be removed with even force,to prevent the concrete profile from being destroyed and prevent the position of truss bar from being changed.After the mortar blocking plate is removed,the concrete at the reserved groove for truss bar shall be under surface finishing,rendering the surface smooth and good-looking.The exposed truss bar at the external sleeper shall be painted by cement paste,to prevent the exposed truss bar from being rusted.

Figure 12 Concrete Pouring and Testing
2.7.9 Steam curing system
The curing falls into steam curing and natural curing.The concrete shall be under steam curing in curing pit upon pouring.The curing process is composed of four stages,i.e.delaying curing,temperature rise,constant temperature and cooling.The automatic temperature controller can adjust the input steam,the temperature and humidity in the curing pit.Figure 13 shows the sleeper curing controller.

Figure 13 Sleeper Curing Controller
The temperature inside the curing pit shall be maintained higher than 5℃in delaying curing stage,and the temperature can only be increased 3 h after pouring.The temperature rise speed shall not be faster than 15℃/h,in cooling control,the core component temperature shall not be over 55℃,the highest temperature inside the pit shall not be over 60℃,and the cooling speed shall not be over 15℃/h.When the temperature difference between the concrete and the ambient temperature is not over 15℃,and the strength of the test-piece curied under same condition reaches 70%(equal to 40 MPa)of the design strength,the formwork can be released.
2.7.10 Formwork removal
When the time for sleeper steam curing meets the requirement,one set of test-piece shall be delivered to laboratory for formwork removal strength test.If the strength is greater than or equal to 40 MPa,the formwork removal strength required by the product,and the temperature difference between the sleeper surface and the ambient temperature is not over 15℃,the sleeper formwork can be released.Figure 14 is the case for sleeper formwork removal.

Figure 14 Sleeper Formwork Removal
The impact air hammer shall be used for formwork removal.In formwork removal process,the sleeper shall fall evenly and shall be confirmed whether they are completely fell off.Rough handling in formwork removal process is prohibited,the sledge hammer must not be used to hammer the formwork,otherwise,either partial formwork may be transformed or the sleeper concrete may be destroyed.The position of the embedded sleeve shall be inspected immediately upon sleeper formwork removal,if the embedded sleeve is destroyed,it shall be repaired promptly.
2.7.11 Natural curing
The natural curing work procedure follows pit out and formwork releasing.The rocker arm sprinkler shall be used to sprinkle water curing in summer season,the curing time provision:the heat-insulating humid-holding curing time for concrete shall not be less than 14 days when the daily average temperature is 10℃≤T<20℃; the heat-insulating humid-holding curing time for concrete shall not be less than 7 days when the daily average temperature is T≥20℃.
The heating system in the workshop shall maintain the indoors temperature not lower than 5℃in winter season.The sleepers after formwork released shall,after the sleeper temperature drops to the ambient temperature,be transported to the storage yard and covered by straw matting for heat preservation.

Figure 15 Sprinkling Water Curing for Sleepers
2.7.12 The pulling resistance testing for embedded sleeves
Three pieces of sleepers shall be randomly selected from those for appearance quality inspection,and one sleeve shall be taken from each sleeper for testing,to test whether there is visible cracks,but little mortar peeling off is allowed.The pulling resistance of the embedded sleeve shall not be less than 60 kN.

Figure 16 Pulling Resistance Test for Sleepers
2.7.13 Static load cracking resistance testing for cross section underneath the bi-block sleepers
The test-pieces are those that have all passed the qualification test for appearance quality and sizes.The test loading device is shown in Figure 17.
The sleeper shall be loaded according to the requirement of appendix A to Temporary Technical Condition for Bi-block Concrete Sleeper of Bi-block Ballastless Track for Passenger Dedicated Railway(Kejiji[2008]No.74):the sleeper shall be put exactly at the center of the press machine,and the loading rate shall not be over 5 kN/s.The pressure acting on the sleeper shall primarily be increased to 90 kN,the sustained load shall begin from 90 kN,and shall be loaded step by step,10 kN for each step.

Figure 17 Static Load Cracking Resistance Testing for Sleepers(Unit:mm)
1.ItshallbeloadedtoP1(kN)untilthefirstcrack appearsvisibletonakedeyes.Generallyspeaking,the crackwidthshallbesmallerthan0.1mm.
2.It shall be loaded to P2(kN)until the crack appears whose width is bigger than 0.2 mm(control width),the load at this time is the allowable value for the component.The concrete crack width under P2shall be recorded.
3.It shall be deloaded slowly from P2to P3(kN),the once appeared control crack will close again.
4.When it is loaded to P4,the crack will expand suddenly,with the width expands to 0.4~0.8 mm.The load at this time refers to the destructive loading value for the component.
5.It shall be loaded to P5(kN),and until can not be loaded again.
If the testing result fails to reach the minimum values of the load control,P1and P2,the test shall be performed again by taking sleepers from the same batch; if the result still fails,the sleeper fabrication shall be tested,even by changing the concrete mixture ratio or by changing different raw materials,until the test examination is passed.
2.7.14 Sleeper ex-factory inspection and assessment
The inspection report for the raw material and the embedded parts of the sleepers shall be checked before getting out of the factory; the overall dimensions and the appearance quality of the sleepers shall be inspected; the concrete quality shall be verified by compressive strength; and the sleepers shall be randomly sampled for static load cracking resistance test,and the embedded sleeves shall be randomly sampled for pull-out test.
In samples drawing,no more than 1 000 pieces of sleepers produced under the same conditions shall be regarded as one batch,from which 8 pieces of sleepers shall be sampled randomly for appearance quality and size testing,3 pieces from the above mentioned 8 pieces of sleepers shall be taken out for static load cracking resistance test and for pull-out test of the embedded sleeves,one end of the sleeper shall be under cracking resistance test,and from the other end one sleeve shall be selected for pull-up test.The cracking resistance test will be assessed as qualified if it is loaded to 90 kN and without crack; the sustained load for pull-up test is 60 kN,and there is no crack visual to naked eyes,which can be regarded as qualified.