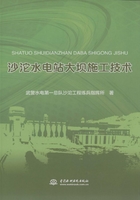
第三节 围堰闭气具体施工方案及方法
大坝土建工程二期右岸导截流后,上游、下游围堰分别填筑至296.0m、294.0m高程作为围堰闭气灌浆施工平台。该高程以下部分作防渗灌浆闭气,以上部分为黏土芯墙防渗。
上、下游围堰防渗闭气灌浆于2007年12月10日开工,于2008年3月18日完工。
一、孔位布置及主要工程量
(一)上游围堰灌浆孔的布置
上游围堰的防渗帷幕灌浆采用一排孔布置,左、右堰头部位三排孔布置,施工过程中对局部较大的渗漏部位再在上游面增加第一排孔(间距为1.0m)。
(二)下游围堰灌浆孔的布置
下游围堰灌浆孔的布置分两部分,右岸深槽部位(右岸46m范围)采用三排孔布置,孔距1.5m,排距1.0m,先施工背水排,再施工迎水排,最后施工中间排。左半部分布置一排孔,孔距1.0m。灌浆孔孔深均为进入基岩1.0m。
(三)主要完成工程量
结合上游、下游围堰钻孔分析后,灵活采取多种防渗闭气灌浆施工方法,取得了良好的闭气效果。完成工程量如下:
上游围堰共钻孔178个共3053.4m,材料:水泥4150t,砂863.7t,水玻璃90.48t,化灌材料225kg,膨润土193t,碱968t,稻草7.337t,海带1.826t。
下游围堰共钻孔239个共5076.9m,材料:水泥3564.9t,砂1024.61t,水玻璃87.293t,锯木粉10.42t。
二、施工总布置
(一)制浆站的设置
上下游分别在围堰防渗轴线内侧、临近纵向混凝土围堰部位搭设水泥平台,建设制浆站。
(1)水泥平台采用φ50mm钢管搭制,长约4m,宽2.5m,上铺设木板,顶设防雨棚。
(2)根据施工工法的需要,分别配备高速搅拌机、高压灌浆机、砂浆泵等组成制、灌浆主系统,同时配备砂浆搅拌机、化学灌浆泵等灌浆设备满足掺和料的添加及双液灌浆需要。
(二)风水电的布置
(1)在上下游围堰制浆站附近各安设移动式空压机1台(上游围堰21m3,下游围堰3.5m3),即满足施工用风的需要。
(2)上下游围堰分别在基坑内安设5.5kW水泵2台(一台备用),抽取基坑内经沉淀后的河水,满足施工用水的需要。
(3)采用动力电缆就近搭接本标供电变压器,满足用电需要。
(三)排污系统的布置
上下游围堰分别在防渗轴线内侧(即靠基坑方向)挖一0.2m×0.2m的积水槽和一0.5m×0.5m×0.5m的积水坑,接受施工中的废水、废浆,待沉淀后,将清水抽排至指定排放点,沉淀物由专人清理并装袋运至弃渣场。
三、主要施工程序及方法
根据上下游围堰不同的地质情况,二期上游围堰的防渗帷幕主要采用控制性水泥灌浆工艺实施,同时利用控制性浆液能顶水上行的水泥灌浆堵漏工艺对局部较大渗漏通道进行封堵施工,控制性水泥灌浆技术及其控制浆液能顶水上行的水泥灌浆堵漏工艺是立足于从灌浆可控性角度出发,结合流体和固体的受力特征,应用水泥浆液加化学外加剂后能使水泥浆液迅速失去流动而变成凝固体的特性,而形成的新的灌浆工艺构思和施工措施。它通过控制水泥浆液的凝胶时间,使水泥浆液在扩散过程中迅速失去流动性,其渗透压力会迅速消失,但水泥结石体还不会产生骨架作用,即软塑体,仍能被挤压滑动,从而有效地控制灌浆升压问题,且不会导致产生浆液流失。该技术就是利用这一原理,使地层产生挤压密实变形和挤压滑动,控制灌浆压力对地层产生的附加压应力值达到足够值后而对地层进行回填置换和挤密、挤实。
二期下游围堰的防渗帷幕主要采用塑性灌浆工艺实施,首先不在浆液中加速凝类材料,而是当浆液消耗达到一定量以后,如果灌浆仍无回浆或压力,根据具体情况加外加剂。
(一)上游围堰施工程序及方法
1.施工程序
针对本工程的实际情况,上游围堰的施工程序主要分为以下四个步骤,即黏土层的挤压密实→堰基部位防渗处理→局部加强→质量检查。施工重点在于第二步,即堰基与河床的接触部位、河床基岩以上部位的防渗处理。
2.0+00.00m桩号(以纵向围堰与横向围堰的交界处为0+00.00桩号)至0+40.10m桩号防渗帷幕灌浆主要工序施工方法
(1)钻孔。
1)采用CM351履带式气动钻车冲击跟管钻进成孔,钻孔孔径为150mm,部分I序孔兼勘探孔钻孔深度为入岩5m,其余孔钻孔深度为入岩1m,若入岩1m发现有不良地质发育则加深孔深,一般处理深度不超过基岩5m,套管要求跟进至入岩1m,“套管法”灌浆,即直接利用套管作为注浆管,在注浆管管口安装盖头连接进浆管和压力表,采用螺杆泵进行自下而上分段、纯压式灌浆工艺。
2)钻孔的孔位、孔向、孔斜等指标按《水工建筑物水泥灌浆施工技术规范》(DL/T 5148—2001)相关要求控制。
3)在钻孔过程中特别注意钻孔的返碴及钻机的运转情况,并根据其返碴及钻机的运转情况进行判断填筑层、河床砂卵石层和基岩深度和厚度。
4)各种地层的钻孔判断:填碴层钻孔一般钻进速度快,时有卡钻现象,返碴岩质、颜色与填筑料的岩质、颜色相一致;砂卵石层一般钻进速度较快,返碴为河砂,比较易于区分;当钻孔遇到大块石分布架空地段时,冲击器运转一般不正常,出现失风或孔间串风、掉钻等现象;钻孔进入基岩后钻进速度一般变慢,冲击器运转一般比较正常,返碴由河砂转为石碴(岩质一般为黑色),持续钻进5m(先导孔)无河砂返出,基本确定为基岩。
(2)灌浆。
1)进行孔底基岩1m下不良地质孔段注浆,达设计压力后,利用拔管机边拔管边灌浆,直至拔至抛填层后,进行河床与基岩接触段灌浆,用砂子对钻孔中揭示的砂砾石层的泥质有机物进行置换后灌浆(砂砾石层的含泥量有机质较多,无法与水泥浆凝结成帷幕体)。河床与基岩接触段灌浆结束后,在继续灌浆的同时缓慢提升套管对抛填层进行灌浆,当拔管过程中出现压力骤然下降或消失时停止拔管,就此进行灌浆。
2)灌浆自下而上分段进行。
3)水泥选用强度等级为32.5的普通硅酸盐水泥,水灰比全部选用0.8∶1一个级配。
4)灌浆压力以进浆管压力控制,各段压力值按标准执行(表2-7)。
5)灌浆结束标准:达到要求灌浆压力且已灌入一定的浆液量后可结束灌浆。
表2-7 灌浆压力表 单位:MPa

(3)特殊情况处理。
1)遇砂砾层、塌孔的处理:用压力水进行冲洗,砂子或混凝土对砂砾石层中的泥质有机质进行置换后灌浆。
2)大耗浆孔段处理:对于吸浆量大的孔段难以结束时(注浆量大于1t/m),可采用浓浆、间歇灌浆、待凝,灌入水泥砂浆(砂子占水泥重量的100%~200%),加入速凝类掺加剂,加入海带、锯木粉、稻草、麻类纤维物等掺和料措施。
(4)质量检查。控制性水泥灌浆的质量检查以压水试验为主,结合取芯检查、基坑渗漏水量综合评定。检查孔数量按总孔数的5%控制。
3.0+40.10m桩号(以纵向围堰与横向围堰的交界处为0+00.00m桩号)至0+87.20m桩号防渗帷幕灌浆主要工序施工方法
0+40.10m桩号(以纵向围堰与横向围堰的交界处为0+00.00m桩号)至0+87.20m桩号防渗帷幕灌浆主要以膏浆灌浆为主要防渗手段,膏浆灌浆孔采用冲击跟管钻进成孔,灌浆采用“套管法”,即直接利用套管作为注浆管,在注浆管管口安装盖头连接进浆管和压力表,采用螺杆泵进行自下而上分段、纯压式灌浆工艺,灌浆分段长度为1.5~3.0m。
上下游排膏浆灌浆按分三序加密的原则进行。先施工下游排,后施工上游排,若下游排堵漏效果好,则可取消对上游排的施工。同排孔先施工Ⅰ序孔,后施工Ⅱ序孔,再施工Ⅲ序孔。其中Ⅰ序孔孔径为150mm,孔间距为4m,其中下游排Ⅰ序孔作为先导孔,用于判断孔下地质情况,孔深要求入岩5m,套管跟随入岩1m后改钻头钻孔,套管不再跟进;Ⅱ序孔孔径为150mm,孔间距为4m,在相邻的两个Ⅰ序孔之间布置,与Ⅰ序孔间距为2m,孔深要求入岩1m;Ⅲ序孔孔径为150mm,孔间距为2m,在相邻的两个Ⅰ序孔和Ⅱ序孔之间布置,距相邻的Ⅰ序孔和Ⅱ序孔的间距为1m,孔深要求入岩1m。
套管法灌浆时,首先进行孔底纯水泥浆注浆,达设计压力后,利用拔管机边拔管边灌浆,直至拔至基岩面后,进行基岩段灌浆。孔底段灌浆结束后,在继续灌浆的同时缓慢提升套管,当拔管长度超过1根套管长度或出现压力骤然下降或消失时停止拔管,就此进行灌浆。
(1)钻孔。
1)钻机就位:采用KR803-1型全液压履带式钻机和MGY-80/100型液压冲击钻机造孔,通过垫木、人工撬板的方式将钻机大致就位,然后将钻机调平,支起支架,采用重锤或地质罗盘仪检测和控制钻机立杆的垂直度,经现场质检人员确认和认可后,方可进行下一道工序施工。
2)开钻:开钻前将钢套管安装到位,检查现场施工各项准备工作是否完成,如钻杆、套管、机械状态、安全防护设施等,全部准备工作完成后,经过现场质检人员认可后开钻,开钻时采用缓慢钻进,钻进1m后进行垂直度检测,若发生偏斜则必须进行调整,以满足孔斜控制要求,没有偏斜则进入正常速度钻孔。
3)钻孔:在钻孔过程中特别注意钻孔的返碴及钻机的运转情况,并根据其返碴及钻机的运转情况进行判断填筑层、河床砂卵石层和基岩深度和厚度。
4)各种地层的钻孔判断:填碴层钻孔一般钻进速度快,时有卡钻现象,返碴岩质、颜色与填筑料的岩质、颜色相一致;砂卵石层一般钻进速度较快,返碴为河砂,比较易于区分;当钻孔遇到大块石分布架空地段时,冲击器运转一般不正常,出现失风或孔间串风、掉钻等现象;钻孔进入基岩后钻进速度一般变慢,冲击器运转一般比较正常,返碴由河砂转为石碴(岩质一般为黑色),持续钻进5m(先导孔)无河砂返出,基本确定为基岩。
5)钻孔记录:先导孔在钻孔过程中,详细、准确记录钻孔时遇到的各种现象,根据返碴情况、钻进速度、钻机及冲击器运转情况判断地层分层深度,大块石的分布、埋深、粒径及地层架空、漏失、串通等情况,钻孔人员通知技术质检人员在现场作出详细记录,以指导下步施工。
当先导孔全部完成后,结合已有的地质剖面,绘制《上游围堰灌浆轴线地质剖面图》,为后续施工提供充实的地质资料,并为后继钻孔控制底高程提供参考依据。
6)终孔:先导孔钻入基岩5m后,停钻终孔。其他各序钻孔根据先导孔钻孔记录绘制的《上游围堰灌浆轴线地质剖面图》确定设计孔深深度,在钻到设计孔深时,根据钻孔速度、冲击器运转情况和孔口返渣确定是否入岩,入岩1m后停钻终孔,未入岩者继续钻进,直至入岩。若入岩高程误差与先导孔揭示的基岩高程差值计算的控制高程差达到3m以上时,按先导孔结束标准进行控制。终孔后进行孔深、孔斜的测量,并做好记录,经过质检人员签字认可后方可最终结束钻孔,移开钻机。
(2)灌浆材料。
1)水泥:采用P.O32.5级的普通硅酸盐水泥。每批水泥要按要求取样进行检测,符合设计要求后方可使用。
2)膨润土:液限大于400%,小于0.08mm的颗粒含量大于80%。必要时加入适量Na2CO3分散剂和CMC增黏剂。
3)水玻璃:模数为2.8~3.5,其浓度采用30~38波美度。
4)掺和料:海带、砂、米石、水玻璃、锯木粉、稻草、麻等纤维物等。
(3)浆液拌制。
1)各类浆液必须搅拌均匀,用比重称测定浆液比重,并做好记录。
2)纯水泥浆液的搅拌时间:使用普通搅拌机时,不少于3min;使用高速搅拌机时,不少于30s。浆液在使用前过筛,从开始制备至用完的时间小于3h。
3)高速搅拌机搅拌转速大于1200r/min,搅拌时间不少于30s。
(4)膏浆浆液。其配方根据现场材料试配出各种流动指标的浆液,并从中优选符合围堰灌浆需求的最佳配比,在施工中根据地层孔隙大小适时调整浆液配比。
(5)浆液变换标准。
1)一般以0.5∶1纯水泥浆液开灌。
2)灌注0.5∶1纯水泥浆液时,灌注量如达到500L,则改用0.5∶1∶0.1配比膏浆灌注。
3)在灌浆总量达到5000L,灌浆管无压力或流量大于50L/min时,采用混合浆进行灌注,混合浆液中的掺料按锯末、稻草、海带顺序(物料粒径逐步增大)掺入,首先掺入锯末,在掺料过程中逐步增加掺量,灌注5min后仍然压力变化不大,再掺入稻草和海带,不得一次掺入过多掺料堵塞灌浆管,随时观察灌浆压力,如果压力仍然无变化,则采用间歇灌浆方式施工,间歇时间为15~30min;如果压力开始上升时,不再掺入掺料,如果吸浆突然停止,及时查明原因,若是堵管(套管),则进行扫孔后恢复灌浆。
4)灌浆压力达到设计标准后开始拔管,在拔管过程中压力丧失为零或下降达到0.05MPa以下时,维持灌浆配比不变继续灌浆,如果有压力,灌浆流量减小,则需回到开灌时的0.5∶1水泥净浆进行灌浆,并按2)、3)、4)的步骤进行浆液变换。
5)灌浆前、浆液变换时、灌浆结束时均应测量浆液密度,灌浆过程中亦应每隔15~30min测量一次浆液密度,并记录在灌浆记录表中。
(6)灌浆压力。Ⅰ、Ⅱ序孔灌浆压力(进浆压力)为0.3~0.5MPa,Ⅲ序孔灌浆压力(进浆压力)为0.5~0.7MPa,可根据灌浆情况及吸浆量大小进行调整。如Ⅲ序孔吸浆量大于5000L,压力无变化时,则灌浆压力可采用Ⅰ、Ⅱ序孔的灌浆压力。
(7)结束标准。Ⅰ、Ⅱ序孔达到了规定的0.2~0.5MPa压力(初始灌浆无压时)且基本不吸浆(吸浆率小于25L/min),或达到规定的灌浆压力,吸浆量仍较大,并采取相应的灌浆措施而灌浆压力仍保持不变,吸浆量已达到4000L时,可以提管20~30cm;Ⅲ序孔达到灌浆压力(进浆压力)0.5MPa、且基本不吸浆(吸浆率小于25L/min)时,即可结束本段灌浆进行拔管,提管15~25cm;孔口返浆,进行封堵加压灌注5min后,可结束本孔灌浆。
(8)特殊情况处理。
1)施工过程中,如遇大块石和孤石,做好详细记录,灌浆时,兼顾空隙大小,及时按浆液的变换标准调整浆液配比,灌浆过程中可采用间歇灌浆、灌混合浆、添加速凝剂等,以控制浆液扩散范围。
2)为防止套管上拔困难,在灌浆起压后每隔30min拔管5cm左右。在间歇灌浆期间,必须活动套管,且要保证在提升过程中孔口有压,严禁在无压的状况下起拔套管。
3)在漂石、块石集中层和龙口段,由于漏浆严重,可调整可控性浆液的流动性能指标,采用较浓膏浆封堵,确保架空部位封堵密实。对于吸浆量特别大的孔段(孔段总注入量大于5000L,仍不起压),可采用提高浆液的速凝性能、掺加纤维材料等方法灌注或不连续灌浆技术进行灌注。
4)灌注膏浆时,灌浆管路的长度一般不得超过20m,如果因孔位布置,需要超过30m的,在使用较浓的膏浆时,可以灌一槽较浓的膏浆,再灌一槽普通膏浆,确保管路的顺畅,如果超过40m,采用接力灌注。
5)灌浆过程中,遇细砂和级配好的地层,吸浆量过小,根据实际情况并报监理工程师批准后,调整浆液配比,采用纯水泥浆液灌注。
6)在被动采用了间歇灌浆(如供浆不及时)或套管被堵时,用冲击钻机在套管内扫孔至灌段段底以下1.0m,再上拔套管10cm左右继续灌注。
(9)灌浆孔回填。每个灌浆孔结束灌浆后,采用浓浆回填钻孔。由于浆液终凝干缩后,在钻孔上部会出现脱空现象,因此,须自原孔位扫孔至干缩浆液顶面后,采用原配比浆液进行回填,直至灌浆孔不再出现脱空,确保防渗帷幕与上部结构物的连接及防渗效果。
(10)废孔处理。凡因故报废的钻孔,均按下列原则进行处理。
1)报废孔应按要求进行封孔,并有封孔记录。
2)在距报废孔20cm的范围内重新开孔。重开孔按技术要求钻进至设计孔深,然后采用套管法自下而上进行灌浆。
3)报废孔的一切原始记录与新开孔的记录资料一并整理归档。
(二)下游围堰施工程序及方法
1.施工流程
围堰灌浆施工工艺流程见图2-5。
图2-5 围堰灌浆施工工艺流程图
2.主要工序施工方法
(1)钻孔布置。钻孔总体考虑单排孔布置,孔距均为1.0m,钻孔轴线布置在下游围堰中心轴线偏下游1m。
(2)工艺参数设置。
1)孔深:设计孔深进入完整基岩1.0~2.0m。
2)灌浆孔距:采用单排布置,孔距均为1.0m。
3)孔径:钻孔直径为150mm。
4)施工次序:设计灌浆孔分为Ⅰ、Ⅱ序进行,在施工中,为更好地探测到漏水深度及宽度,每6~8m布置一个孔,再依次加密,最后形成一道完整的防渗幕墙。
5)灌浆压力:灌浆压力的确定一般根据水头大小而设计。按照所承受的水头大小确定Ⅰ序孔灌浆压力,Ⅰ序孔灌浆压力设计为最高洪水位相应的水头压力,Ⅱ序孔在Ⅰ序孔的基础上提高20%左右。暂定灌浆压力为:Ⅰ序孔:0.15MPa;Ⅱ序孔:0.18MPa。实际灌浆过程中,可能出现孔口冒浆等情况发生而不能达到灌浆压力,因此当冒浆位置距离灌浆孔1.5m以外并冒浓浆后该灌浆孔可以结束灌浆。
6)水灰比:由于漏水带地层比较复杂,渗漏间隙及水头差大,使用浓砂浆(或者混合浆液、膏浆及加化学外加剂)进行灌注Ⅰ序孔,将主要空隙充填,然后再用稀浆对小的渗水点进行封堵灌注。建议Ⅰ序孔采用水灰砂比为0.5∶1∶0.5~0.5∶1∶1的浓砂浆进行灌注;Ⅱ序孔首先采用0.5∶1的纯水泥浆开灌,根据情况变为高效速凝混合砂浆灌注。外加剂:砂掺量为水泥量的40%~80%,水玻璃掺量为水泥量的3%~5%,锯末掺量为水泥量的5%~15%,还有速凝剂和聚氨酯等。
(3)钻孔工艺。全孔采用风动潜孔钻偏心跟管钻进。钻孔直径一般在150mm。钻机使用潜孔钻机进行钻孔。每台钻机需配置20m3/min空压机供风,配备必要的钻杆及套管。钻孔结束后,待灌浆射浆管路安装完毕后,使用拔管机将孔内套管拔出。根据实际情况如:成孔难度较大,可待灌浆返浆后再拔套管。
(4)灌浆方法。利用套管作为孔口管,结合地层渗漏程度,采用“孔底循环、孔口封闭灌浆”的方法进行处理,一般分段段长控制在1.5~3.0m。
(三)右岸堰头的渗漏通道的处理
根据右岸堰头的地质条件,上下游围堰均存在河水绕右岸堰头山体渗漏的可能性,基坑抽水后,一经发现绕渗情况,采取以下措施进行处理。
(1)在右堰头部位增设6~8个斜孔,进行灌浆封堵。
(2)在右岸堰头山体上增设灌浆孔,进行灌浆封堵。
(四)围堰底部渗漏通道的处理
根据地质条件分析,类似纵向围堰子堰底部溶蚀深槽渗漏情况,在上下游围堰中也极有可能发生,采取的应对措施为:
(1)通过部分I序孔兼勘探孔的钻孔施工,进一步探明防渗轴线下基岩内的地质情况。
(2)一经发现防渗轴线下基岩内存在可能产生渗漏的溶蚀裂隙或破碎层,立即报告监理人,并按监理人的指示执行。
(3)进入基岩1.0m之外的所有钻孔、灌浆等作业,已超出本合同项目的工作范畴,如需施工,随即启动工程变更程序。
四、施工过程中采取的措施
在实际施工过程中,上游、下游围堰各分为4个单元,由于闭气灌浆施灌前,工期较紧,作业面上施工队伍及机具较多,施工场地受到限制,故未做钻孔取芯等地堪复查工作来判定帷幕底线以及堰基地层地质条件。
在实际施工中,根据造孔难度大、易塌孔等困难,采用了跟管钻进,拨管,自下而上进行灌浆的施工工艺,大大提高了造孔的成功率和灌浆效果。
根据设计图纸,一排孔施工完后在基坑抽水时水位下降缓慢,经业主、设计、监理和施工四方现场分析后认为:深槽部位一排孔难以形成防渗体,研究后决定深槽段增加一排加强孔,在钻孔时试探性地钻穿34.9m基岩后发现下面还有一层砂砾石,继续加深钻至下一层基岩,钻孔深度基本上达到40m左右。
二期上下游围堰主要工程量及质量自查见表2-8。
表2-8 二期上下游围堰防渗灌浆质量自查表
